Material used in ballscrew
A ball screw and element technology, applied in belts/chains/gears, mechanical equipment, transmissions, etc., to achieve the effect of improving internal organizational structure, social and economic benefits, and improving quenching brittleness and deformation
- Summary
- Abstract
- Description
- Claims
- Application Information
AI Technical Summary
Problems solved by technology
Method used
Image
Examples
Embodiment 1
[0038] A material for ball screw according to the present invention, wherein the active ingredients and weight percentage are: 0.58% of carbon element, 0.80% of manganese element, 0.015% of phosphorus element, 0.015% of sulfur element, 0.35% of silicon element, chromium 0.25% element, 0.20% copper element, 0.10% molybdenum element, 0.20% nickel element, 0.05% vanadium element, 0.040% aluminum element, and the balance is iron element. According to the above composition and weight percentage, it is smelted by adopting electric arc furnace plus vacuum refining method, and finally smelted into steel in the state of hot-rolled spheroidizing annealing and peeling.
Embodiment 2
[0040] A material for a ball screw according to the present invention, wherein the active ingredients and weight percentage are: 0.605% of carbon element, 0.65% of manganese element, 0.015% of phosphorus element, 0.015% of sulfur element, 0.35% of silicon element, chromium 0.25% element, 0.20% copper element, 0.10% molybdenum element, 0.20% nickel element, 0.05% vanadium element, 0.040% aluminum element, and the balance is iron element. According to the above composition and weight percentage, it is smelted by adopting electric arc furnace plus vacuum refining method, and finally smelted into steel in the state of hot-rolled spheroidizing annealing and peeling.
Embodiment 3
[0042] A material for ball screw according to the present invention, wherein the active ingredients and weight percentage are: 0.63% of carbon element, 0.50% of manganese element, 0.015% of phosphorus element, 0.015% of sulfur element, 0.35% of silicon element, chromium 0.25% element, 0.20% copper element, 0.10% molybdenum element, 0.20% nickel element, 0.05% vanadium element, 0.040% aluminum element, and the balance is iron element. According to the above composition and weight percentage, it is smelted by adopting electric arc furnace plus vacuum refining method, and finally smelted into steel in the state of hot-rolled spheroidizing annealing and peeling.
[0043] Through the above-mentioned technical scheme, the steel smelted from this material by adding alloy elements completely overcomes the weakness of GCr15 steel, improves the internal structure of the steel, and makes it easy to cut and roll on the basis of maintaining the advantages of GCr15 steel , improved quenchin...
PUM
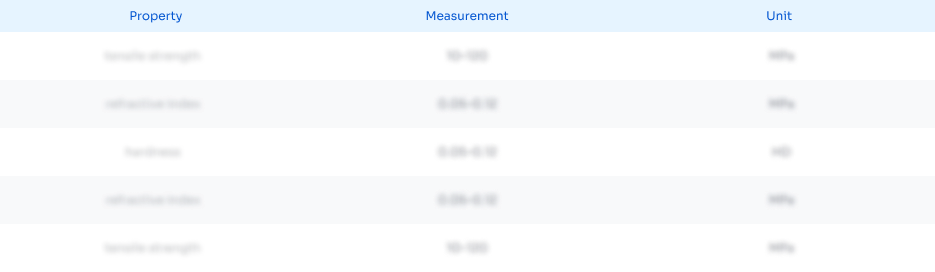
Abstract
Description
Claims
Application Information

- R&D
- Intellectual Property
- Life Sciences
- Materials
- Tech Scout
- Unparalleled Data Quality
- Higher Quality Content
- 60% Fewer Hallucinations
Browse by: Latest US Patents, China's latest patents, Technical Efficacy Thesaurus, Application Domain, Technology Topic, Popular Technical Reports.
© 2025 PatSnap. All rights reserved.Legal|Privacy policy|Modern Slavery Act Transparency Statement|Sitemap|About US| Contact US: help@patsnap.com