Infrared radiation coating capable of forming coating with low conductivity factor
A technology of infrared radiation coating and low thermal conductivity, which is applied in the field of infrared radiation energy-saving materials, can solve problems such as poor infrared radiation performance and poor high temperature stability, and achieve excellent infrared radiation performance, excellent low thermal conductivity, and high infrared radiation performance effect
- Summary
- Abstract
- Description
- Claims
- Application Information
AI Technical Summary
Problems solved by technology
Method used
Image
Examples
Embodiment 1
[0022] In terms of mass percentage, it is 40% of spinel-silicate multiphase composite system infrared radiation powder, 5% of pore-forming agent, 10% of potassium hexatitanate, 30% of water glass, 5% of water, and 6.7% of inorganic bonding agent , organic bentonite 1%, sodium phosphate 2%, tributyl phosphate 0.2%, water-based acrylic resin 0.1%, the pore-forming agent is composed of graphite and starch, and the mass ratio of graphite and starch is 50%: 50% , Weigh the above-mentioned components, stir and mix for 4 hours, and then obtain the infrared radiation coating of viscous suspending fluid.
[0023] Among them, the infrared radiation powder of the spinel-silicate multi-phase composite system includes the A component forming the spinel solid solution, the B component forming the silicate mineral and the accelerator C component, wherein the The above-mentioned A component includes Fe 2 o 3 , MnO 2 , CuO and Mo 2 o 3 , the B component includes Al 2 o 3 , SiO 2 , MgO ...
Embodiment 2
[0029] According to the mass ratio, 30% spinel-silicate multiphase composite system infrared radiation powder, 3% pore forming agent, 20% potassium hexatitanate, 25% water glass, 10% water, 8% inorganic bonding agent , 2% organic bentonite, 1% sodium phosphate, 0.5% tributyl phosphate, 0.5% water-based acrylic resin, the above-mentioned various components are weighed according to the proportion, and the described pore-forming agent is composed of graphite and starch. The mass ratio of starch and starch is 50%:50%. Stir and mix for 1 hour to obtain a viscous suspension fluid infrared radiation coating.
[0030] Among them, the mass ratio of each component in the infrared radiation powder of the spinel-silicate multiphase composite system is: 28%MnO 2 , 12%CuO, 6%Mo 2 o 3 , 5%V 2 o 5 、5%WO 3 , 5%Al 2 o 3 , 20%SiO2 2 , 10%MgO, 6%TiO 2 and 3% CaO; the preparation process is as follows: batching various raw materials according to the specified ratio, ball milling, mixing, ...
Embodiment 3
[0035] According to the mass ratio, it is 50% spinel-silicate multiphase composite system infrared radiation powder, 3% pore forming agent, 33% water glass, 10% water, 1% inorganic bonding agent, 1% organic bentonite, 1% % tributyl phosphate, 1% water-based acrylic resin, the above-mentioned various components are weighed according to the proportion, stirred and mixed for 3 hours, and the infrared radiation coating of viscous suspension fluid is obtained.
[0036] Among them, the mass ratio of each component in the infrared radiation powder of the spinel-silicate multiphase composite system is: 10% Fe 2 o 3 , 60%MnO 2 , 3%CuO, 4%Co 2 o 3 , 3%NiO, 2%WO 3 , 8%Al 2 o 3 , 5%SiO2 2 , 3% BaO and 2% CaO; the preparation process is as follows: batching various raw materials according to the specified ratio, ball milling, mixing, drying and pressing the ingredients into a block green body; During the process, first heat to 800°C for 6 hours to form a spinel solid solution, and ...
PUM
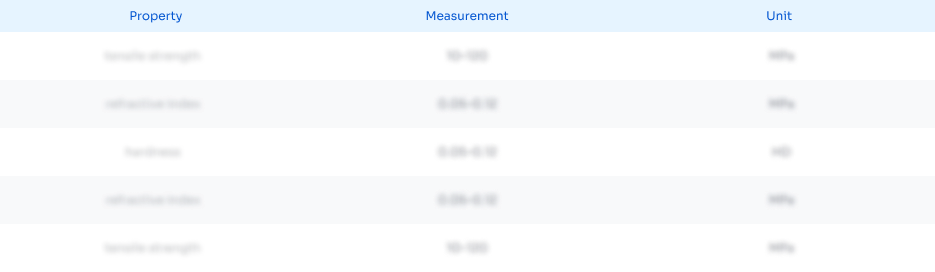
Abstract
Description
Claims
Application Information

- Generate Ideas
- Intellectual Property
- Life Sciences
- Materials
- Tech Scout
- Unparalleled Data Quality
- Higher Quality Content
- 60% Fewer Hallucinations
Browse by: Latest US Patents, China's latest patents, Technical Efficacy Thesaurus, Application Domain, Technology Topic, Popular Technical Reports.
© 2025 PatSnap. All rights reserved.Legal|Privacy policy|Modern Slavery Act Transparency Statement|Sitemap|About US| Contact US: help@patsnap.com