Active agent for laser welding of ferrite stainless steel and using method for active agent
An active agent, stainless steel technology, used in laser welding equipment, welding media, welding equipment and other directions, can solve the problems of increasing weld penetration, shallow weld penetration of ferritic stainless steel laser welding, low welding efficiency, etc. Absorption rate, ideal coating effect, and the effect of improving welding efficiency
- Summary
- Abstract
- Description
- Claims
- Application Information
AI Technical Summary
Problems solved by technology
Method used
Image
Examples
Embodiment 1
[0044] Weigh 5 parts of ZrO in parts by weight with an electronic balance 2 , 1 part of CaO, 2.8 parts of MgO and 1.2 parts of CaCO 3 , mixed, and fully ground to make the active agent. Take an appropriate amount of the active agent of the mixed components in a clean beaker, add 0.5 part of its weight in absolute ethanol to make a paste, and then use a flat brush to evenly coat the surface of the steel plate to be welded, and the thickness of the coating is just enough to cover the metal surface Gloss is preferred. Before activator coating, the steel plate to be welded needs to be polished with 240# metallographic sandpaper and cleaned with absolute ethanol to remove surface oil. After the coating layer is dry, laser welding is carried out using the welding specifications shown in Table 1 below.
[0045] Table 1 Specifications for active laser welding
[0046]
Embodiment 2
[0048] Weigh 5.8 parts of ZrO in parts by weight with an electronic balance 2 , 1.5 parts of CaO, 1.2 parts of MgO and 1.6 parts of CaCO 3 , mixed, and fully ground to make the active agent. Take an appropriate amount of mixed active agent in a clean beaker, add 0.3 part of its weight in absolute ethanol to make a paste, and then use a flat brush to evenly coat the surface of the steel plate to be welded, and the thickness of the coating is just enough to cover the metal surface Gloss is preferred. Before activator coating, the steel plate to be welded needs to be polished with 240# metallographic sandpaper and cleaned with absolute ethanol to remove surface oil. After the coating layer is dry, laser welding is carried out using the welding specifications shown in Table 1 below.
Embodiment 3
[0050] Weigh 7 parts of ZrO in parts by weight with an electronic balance 2 , 0.9 parts of CaO, 0.4 parts of MgO and 1.7 parts of CaCO 3 , mixed, and fully ground to make the active agent. Take an appropriate amount of mixed active agent in a clean beaker, add 0.6 parts of acetone equivalent to its weight to make a paste, and then use a flat brush to evenly coat the surface of the steel plate to be welded. The thickness of the coating is just enough to cover the gloss of the metal surface. should. Before activator coating, the steel plate to be welded needs to be polished with 240# metallographic sandpaper and cleaned with absolute ethanol to remove surface oil. After the coating layer is dry, laser welding is carried out using the welding specifications shown in Table 1 below.
PUM
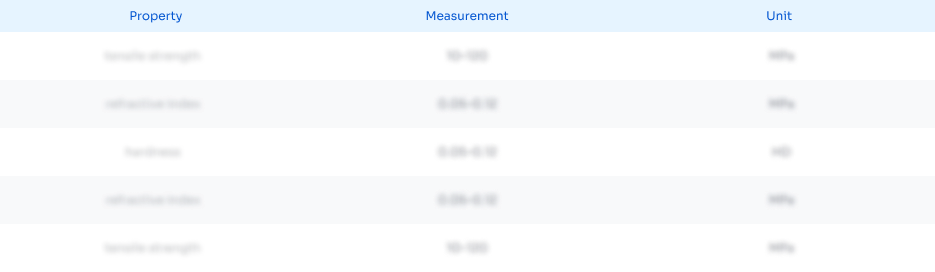
Abstract
Description
Claims
Application Information

- Generate Ideas
- Intellectual Property
- Life Sciences
- Materials
- Tech Scout
- Unparalleled Data Quality
- Higher Quality Content
- 60% Fewer Hallucinations
Browse by: Latest US Patents, China's latest patents, Technical Efficacy Thesaurus, Application Domain, Technology Topic, Popular Technical Reports.
© 2025 PatSnap. All rights reserved.Legal|Privacy policy|Modern Slavery Act Transparency Statement|Sitemap|About US| Contact US: help@patsnap.com