Slip frequency vector control method for asynchronous motor
A technology of slip frequency and vector control, which is applied in vector control system, motor generator control, electronic commutation motor control, etc., and can solve problems such as inaccurate control
- Summary
- Abstract
- Description
- Claims
- Application Information
AI Technical Summary
Problems solved by technology
Method used
Image
Examples
Embodiment Construction
[0018] Below in conjunction with accompanying drawing and specific embodiment the present invention is described in detail:
[0019] As shown in the figure: IM represents asynchronous motor, the present invention provides a kind of asynchronous motor slip frequency vector control method, it comprises the following steps:
[0020] Step 1. Parameter initialization; after the inverter is powered on, the parameter initialization is completed, and the motor parameters and control parameters in the motor control are set. In the commonly used slip frequency vector control system, the speed loop and current loop double closed-loop control strategy is adopted. , the system has a set of preset motor parameters, including stator side and rotor side, which can be provided by the motor manufacturer or obtained from the motor nameplate.
[0021] Step 2. Sampling the three-phase stator current of the motor and detecting the angular velocity of the motor ω r ; Feedback motor angular velocity...
PUM
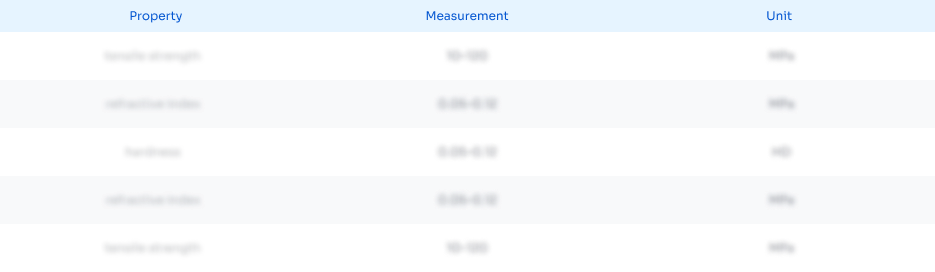
Abstract
Description
Claims
Application Information

- Generate Ideas
- Intellectual Property
- Life Sciences
- Materials
- Tech Scout
- Unparalleled Data Quality
- Higher Quality Content
- 60% Fewer Hallucinations
Browse by: Latest US Patents, China's latest patents, Technical Efficacy Thesaurus, Application Domain, Technology Topic, Popular Technical Reports.
© 2025 PatSnap. All rights reserved.Legal|Privacy policy|Modern Slavery Act Transparency Statement|Sitemap|About US| Contact US: help@patsnap.com