Method for enhancing total mercury recovery rate of metallurgical fume by reducing bivalent mercury
A recovery rate, divalent mercury technology, applied in separation methods, chemical instruments and methods, dispersed particle separation, etc., can solve problems such as difficult recycling of mercury and sulfur, secondary pollution, high operating costs, etc., to achieve an increase in total mercury Effects of recovery rate, increased equipment cost, and waste treatment cost savings
- Summary
- Abstract
- Description
- Claims
- Application Information
AI Technical Summary
Problems solved by technology
Method used
Image
Examples
Embodiment 1
[0035] A glass bubbling device with a volume of 500 mL was used as the main reactor, and the liquid volume in the reactor was kept at about 250 mL. (1) Add 250mL concentration of mercuric chloride solution that is 100mg / L in the reactor; Inject 10mL concentration and be 184mM / L sodium sulfite solution in the reactor; Air flow is controlled at 1L / min, after 20 minutes of reaction, react Determination of Hg of the solution in the vessel with a cold atomic absorption mercury analyzer 2+ The remaining amount, according to which the reduced Hg is calculated 2+ Quantity and reduction rate; tail gas is absorbed with 5% potassium permanganate solution; the total power of the device is provided by the air pump. After adopting the above method, Hg 2+ The reduction rate can be 85% or above. (2) Under the same mercuric chloride solution condition, inject 1mL concentration into the solution and be 184mM / L sodium sulfite solution, after 30 minutes of reaction, measure Hg 2+ The remainin...
Embodiment 2
[0038] Utilize an internal diameter of 100mm, a long 1200mm plexiglass material wet scrubber as the main reactor, (1) add 800mL concentration of mercuric chloride solution that is 100mg / L in the reactor; The spray concentration is 1.84mM / L sodium sulfite solution for 20 minutes; after 20 minutes of reaction, the solution in the reactor is measured with a cold atomic absorption mercury meter to measure Hg 2+ The remaining amount, according to which the reduced Hg is calculated 2+ Amount and reduction rate; tail gas is absorbed with 5% potassium permanganate. After adopting the above method, Hg 2+ The reduction rate can be 85% or above. (2) Add 800mL concentration of mercuric chloride solution that is 100mg / L in the reactor; Spray concentration is 0.7mM / L sodium sulfite and 1.2mM / L sodium bisulfite mixed solution 20 in the reactor with the flow rate of 160mL / min Minutes; After 20 minutes of reaction, the solution in the reactor was measured with a cold atomic absorption mercu...
Embodiment 3
[0040] Using sulfite (SO 3 2- ), bisulfite (HSO 3 - ) or a mixture of the two, divalent mercury (Hg 2+ ) is reduced to zero-valent mercury (Hg 0 ) method, device such as figure 1 As shown, it specifically includes the following steps:
[0041] 1. Distribute one flue gas from the flue gas system, pass it from the diverted flue gas inlet 1 into the NaOH washing tower 2 (dilute NaOH is the detergent), and use the pump 4 to spray the NaOH washing liquid from the NaOH storage tank 3 into the NaOH scrubber 2 to make the SO in the flue gas 2 React with NaOH to produce SO 3 2- 、HSO 3 - or a mixture of both.
[0042] 2. The split flue gas enters the main flue gas pipeline from the outlet 6 of the NaOH scrubber 2, and the SO in the NaOH scrubber 2 3 2- 、HSO 3 - Or the mixed solution of the two is transported in the acid liquid washing liquid tank 10 by pump 5;
[0043] 3. The main flue gas enters the pickling tower 8 from the inlet 7, and uses the pump 9 to spray the was...
PUM
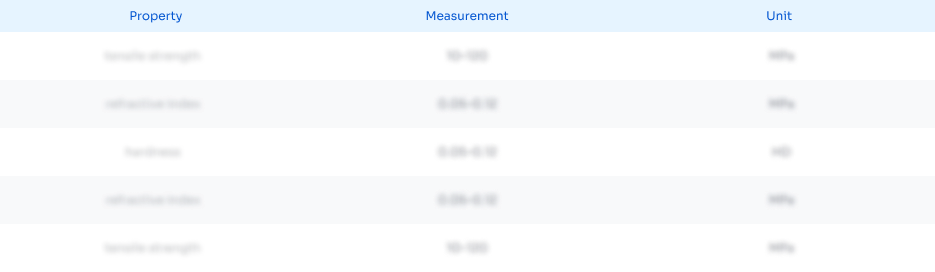
Abstract
Description
Claims
Application Information

- R&D
- Intellectual Property
- Life Sciences
- Materials
- Tech Scout
- Unparalleled Data Quality
- Higher Quality Content
- 60% Fewer Hallucinations
Browse by: Latest US Patents, China's latest patents, Technical Efficacy Thesaurus, Application Domain, Technology Topic, Popular Technical Reports.
© 2025 PatSnap. All rights reserved.Legal|Privacy policy|Modern Slavery Act Transparency Statement|Sitemap|About US| Contact US: help@patsnap.com