Method for preparing NiO/SmBiO3 composite buffer layer thin film of high-temperature super-conduction coating conductor on biaxially-textured NiW alloy substrate
A composite buffer layer and high-temperature superconducting technology, applied in the manufacture/processing of superconductor devices, etc., can solve the problems of complex buffer layer process, high cost, and unsuitability for large-scale deposition, and achieve suitable for large-scale deposition, low cost, and The effect of improving texture
- Summary
- Abstract
- Description
- Claims
- Application Information
AI Technical Summary
Problems solved by technology
Method used
Image
Examples
Embodiment 1
[0029] The preparation method of this example consists of the following steps in turn:
[0030] a. Surface corrosion modification of the NiW alloy substrate: after the annealed biaxially textured NiW alloy (200) substrate has been washed with alcohol and acetone, it is suspended and dipped in a diluted nitric acid solution with a concentration of 30% for 40, Take it out, wash it, and let it dry. Then suspend and immerse it in a mixed modification solution prepared with 150 volumes of hydrogen peroxide and 1 volume of ammonia water for 20 seconds, take it out, wash it, and dry it in the air;
[0031] b. Oxidation heat treatment: Rapidly raise the temperature of the tubular atmosphere sintering furnace to 740°C. When the temperature and the flow rate of the atmosphere are stable, push the corroded and modified NiW alloy (200) substrate into the furnace. After the time in the process reaches 50 minutes, the oxidized base tape is pushed out from the furnace and cooled to room tem...
Embodiment 2
[0038] NiO / SmBiO3 Composite buffer layer preparation steps are:
[0039] a. Surface corrosion modification of the NiW alloy substrate: after the annealed biaxially textured NiW alloy (200) substrate, after being washed with alcohol and acetone successively, it is suspended and immersed in a diluted nitric acid solution with a concentration of 40% for 60s. Take it out, wash it, and let it dry. Then suspend and immerse it in a mixed modification solution prepared with 150 volumes of hydrogen peroxide and 2 volumes of ammonia water for 40 seconds, take it out, wash it, and dry it in the air;
[0040] b. Oxidation heat treatment: Rapidly raise the temperature of the tubular atmosphere sintering furnace to 770°C. When the temperature and the flow rate of the atmosphere are stable, push the corroded and modified NiW alloy (200) substrate into the furnace. After the time in the process reaches 40 minutes, the oxidized base tape is pushed out from the furnace and cooled to room tempe...
Embodiment 3
[0047] NiO / SmBiO3 Composite buffer layer preparation steps are:
[0048] a. Surface corrosion modification of the NiW alloy substrate: after the annealed biaxially textured NiW alloy (200) substrate, after being washed with alcohol and acetone successively, it was suspended and dipped in a diluted nitric acid solution with a concentration of 50% for 120s. Take it out, wash it, and let it dry. Then suspend and immerse it in a mixed modification solution prepared with 150 volumes of hydrogen peroxide and 4 volumes of ammonia water for 60 seconds, take it out, wash it, and dry it in the air;
[0049] b. Oxidation heat treatment: Rapidly raise the temperature of the tubular atmosphere sintering furnace to 800°C. When the temperature and the flow rate of the atmosphere are stable, push the corroded and modified NiW alloy (200) substrate into the furnace. After the time in the process reaches 20 minutes, the oxidized base tape is pushed out from the furnace and cooled to room tempe...
PUM
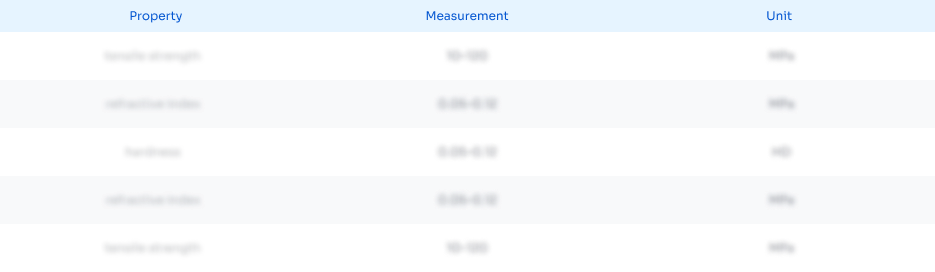
Abstract
Description
Claims
Application Information

- R&D
- Intellectual Property
- Life Sciences
- Materials
- Tech Scout
- Unparalleled Data Quality
- Higher Quality Content
- 60% Fewer Hallucinations
Browse by: Latest US Patents, China's latest patents, Technical Efficacy Thesaurus, Application Domain, Technology Topic, Popular Technical Reports.
© 2025 PatSnap. All rights reserved.Legal|Privacy policy|Modern Slavery Act Transparency Statement|Sitemap|About US| Contact US: help@patsnap.com