Inversed LED (Light Emitting Diode) chip structure and preparation method of inversed LED chip
A LED chip and flip-chip technology, applied in the direction of electrical components, circuits, semiconductor devices, etc., can solve the problems of poor chip reliability, making electrode patterns, and reduced light efficiency, so as to achieve improved performance, good support, and increased reliability. Effect
- Summary
- Abstract
- Description
- Claims
- Application Information
AI Technical Summary
Problems solved by technology
Method used
Image
Examples
Embodiment 1
[0092] On the growth substrate made of sapphire, a buffer layer made of GaN, an N-type semiconductor layer made of GaN, an active layer made of InGaN and a P-type semiconductor layer made of GaN are sequentially deposited by metal-organic chemical vapor deposition;
[0093] Depositing a first metal intermediate layer composed of Ni / Ag / Ti / W / Au / Sn elements on the surface of the P-type semiconductor layer made of GaN;
[0094] A second metal interlayer made of Au / Sn elements is deposited on a silicon alloy transfer substrate with a silicon content of 80 wt % and an aluminum content of 20 wt %. The silicon alloy material with a silicon content of 80wt% and an aluminum content of 20wt% has a thermal expansion coefficient similar to that of sapphire;
[0095] The first metal intermediate layer and the second metal intermediate layer are bonded in a vacuum thermocompression in opposite directions, so that the first metal intermediate layer and the second metal intermediate layer diff...
Embodiment 2
[0109]On the growth substrate made of sapphire, a buffer layer made of GaN, an N-type semiconductor layer made of GaN, an active layer made of InGaN and a P-type semiconductor layer made of GaN are sequentially deposited by metal-organic chemical vapor deposition;
[0110] Depositing a first metal intermediate layer made of Ag / Ti / Au / Sn elements on the surface of the P-type semiconductor layer made of GaN;
[0111] A second metal interlayer made of Au / Sn elements is deposited on a silicon alloy transfer substrate with a silicon content of 50 wt%, an aluminum content of 40 wt%, and a copper content of 10 wt%.
[0112] The first metal intermediate layer and the second metal intermediate layer are bonded in a vacuum thermocompression in opposite directions, so that the first metal intermediate layer and the second metal intermediate layer diffuse each other to form a metal alloy. The parameters of vacuum thermocompression bonding include: the gas pressure is 1torr, the temperature...
PUM
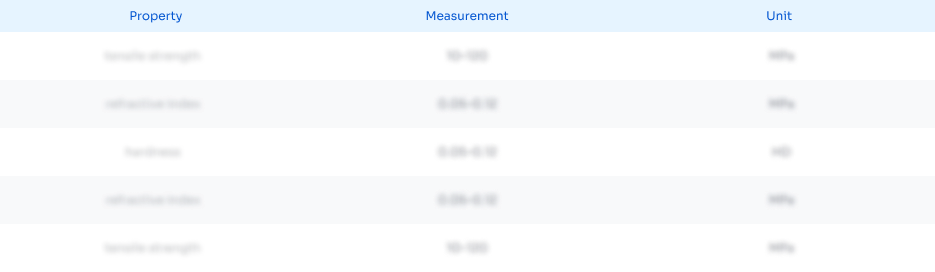
Abstract
Description
Claims
Application Information

- Generate Ideas
- Intellectual Property
- Life Sciences
- Materials
- Tech Scout
- Unparalleled Data Quality
- Higher Quality Content
- 60% Fewer Hallucinations
Browse by: Latest US Patents, China's latest patents, Technical Efficacy Thesaurus, Application Domain, Technology Topic, Popular Technical Reports.
© 2025 PatSnap. All rights reserved.Legal|Privacy policy|Modern Slavery Act Transparency Statement|Sitemap|About US| Contact US: help@patsnap.com