Preparation method of halogen-free flame-retardant toughening polypropylene composite material
A composite material, polypropylene technology, applied in the field of polypropylene composite material preparation, can solve the problem of reducing the flame retardant performance and thermal stability performance of the composite material system, the processing performance of the composite material, the negative impact of mechanical properties, and the deterioration of the mechanical toughness of the matrix polymer. and other problems, to achieve the effect of overcoming the decline of mechanical toughness, good processing performance and low production cost
- Summary
- Abstract
- Description
- Claims
- Application Information
AI Technical Summary
Problems solved by technology
Method used
Image
Examples
Embodiment 1
[0020] A specific embodiment of the present invention is a preparation method of a halogen-free flame-retardant toughened polypropylene composite material, the specific method of which is as follows:
[0021] 1. Put 100 parts of dried magnesium hydroxide in a high-speed stirrer, then spray 2.0 parts of silane coupling agent on the surface of magnesium hydroxide, and stir for 30 minutes at a temperature of 100°C. Be 2000rpm, obtain modified magnesium hydroxide;
[0022] II, the modified magnesium hydroxide that step I obtains and 80 parts of weight dry polypropylenes, 18 parts weight dry polyolefin elastomers, 2.0 parts weight polyolefin elastomer graft maleic anhydride-styrene, 0.05 parts Heavy antioxidant, 0.1 part of heavy lubricant, placed in a mixer and mixed uniformly to obtain a compound;
[0023] III. Mix and granulate the mixture obtained in step II in a twin-screw extruder, dry the extruded pellets and inject them on an injection molding machine.
Embodiment 2
[0025] A method for preparing a halogen-free flame-retardant and toughened polypropylene composite material, the specific method of which is:
[0026] 1. Place 100 parts of dried magnesium hydroxide in a high-speed stirrer, then spray 2.0 parts of silane coupling agent on the surface of magnesium hydroxide, and stir for 25 minutes at a temperature of 80°C. Be 1800rpm, obtain modified magnesium hydroxide;
[0027] II, the modified magnesium hydroxide that step I obtains and 79 parts by weight of dry polypropylene, 20 parts of weight of dry polyolefin elastomer, 1.0 part of weight of polyolefin elastomer grafted maleic anhydride-styrene, 0.05 part Heavy antioxidant 0.1 part of heavy lubricant is placed in a mixer and mixed evenly to obtain a compound;
[0028] III. Mix and granulate the mixture obtained in step II in a twin-screw extruder, dry the extruded pellets and inject them on an injection molding machine.
Embodiment 3
[0030] A method for preparing a halogen-free flame-retardant and toughened polypropylene composite material, the specific method of which is:
[0031] 1. Place 100 parts of dried magnesium hydroxide in a high-speed stirrer, then spray 2.0 parts of silane coupling agent on the surface of magnesium hydroxide, and stir for 35 minutes at a temperature of 120°C. Be 1500rpm, obtain modified magnesium hydroxide;
[0032] II, the modified magnesium hydroxide that step I obtains and 80 parts by weight of dry polypropylene, 18.5 parts of weight of dry polyolefin elastomer, 1.5 parts of weight of polyolefin elastomer graft maleic anhydride-styrene, 0.05 part Heavy antioxidant 0.1 part of heavy lubricant is placed in a mixer and mixed evenly to obtain a compound;
[0033] III. Mix and granulate the mixture obtained in step II in a twin-screw extruder, dry the extruded pellets and inject them on an injection molding machine.
PUM
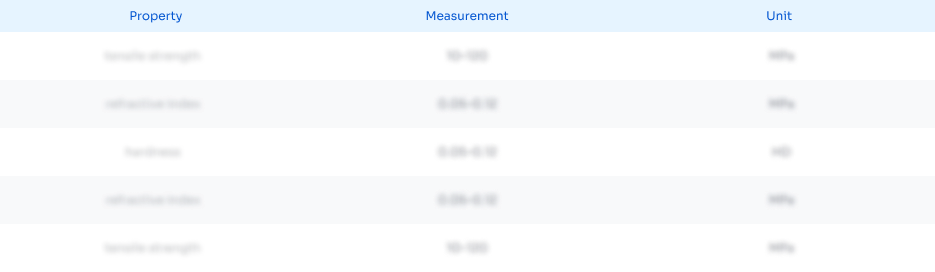
Abstract
Description
Claims
Application Information

- R&D
- Intellectual Property
- Life Sciences
- Materials
- Tech Scout
- Unparalleled Data Quality
- Higher Quality Content
- 60% Fewer Hallucinations
Browse by: Latest US Patents, China's latest patents, Technical Efficacy Thesaurus, Application Domain, Technology Topic, Popular Technical Reports.
© 2025 PatSnap. All rights reserved.Legal|Privacy policy|Modern Slavery Act Transparency Statement|Sitemap|About US| Contact US: help@patsnap.com