Iron-containing solid byproduct of iron making by smelting reduction and manufacturing method thereof
A production method and by-product technology, which are applied in the field of smelting reduction iron-smelting iron-containing solid by-products and their production fields, can solve problems such as inability to meet strength requirements, and achieve the effects of realizing the cost of molten iron, avoiding a large amount of accumulation, and increasing the output of molten iron.
- Summary
- Abstract
- Description
- Claims
- Application Information
AI Technical Summary
Problems solved by technology
Method used
Image
Examples
Embodiment 1
[0051] Gas mud: iron ore sieve powder: dust removal powder (dry basis, weight) 20%: 75%: 5%, binder, added, 10%, water, added, adjusted to 8%. The above-mentioned materials are mixed, and the mixture is pressed by a hydraulic molding machine. The pressure of the molding machine is 10 MPa, and the pressurization time is 10s. It is placed in the air for natural curing for 28 days. The binder is 90% ordinary Portland cement + 10% high alumina cement, and the particle size of the iron ore under-sieve powder is less than 6.3mm, and the content greater than 1mm is 70%.
[0052] After curing, the compressive strength of the agglomerates is 1920N / piece, and the strength reaches the metallurgical standard YB / T005-2005 secondary iron pellet ore standard, which meets the strength requirements for directly adding to the gasifier (>1800N / piece). It can be fed into the gasifier together with lump coal and coke through the coal spiral. Calculated by using 300 tons of agglomerates per day, 13...
Embodiment 2
[0054] Gas mud: iron ore sieve powder: dust removal powder (dry basis, weight) 37%: 60%: 3%, binder, added, 18%, water, added, adjusted to 11%. The above-mentioned materials are mixed, and the mixture is pressed by a hydraulic molding machine. The pressure of the molding machine is 10 MPa, and the pressurization time is 10s. It is placed in the air for natural curing for 28 days. The binder is 80% ordinary Portland cement + 20% slag cement, and the particle size of the iron ore under-sieve powder is less than 6.3mm, and the content of the powder greater than 1mm is 70%.
[0055] After curing, the compressive strength of the agglomerates is 1956N / piece, and the strength reaches the metallurgical standard YB / T005-2005 second-grade iron pellet ore standard, meeting the strength requirements for directly adding to the gasifier (>1800N / piece). It can be fed into the gasifier together with lump coal and coke through the coal spiral. Calculated by using 300 tons of agglomerates a day...
Embodiment 3
[0057] Gas mud: iron ore sieve powder: dust removal powder (dry basis, weight) 43%: 53%: 4%, binding agent, add, 22%, water, add, adjust to 12%. The above-mentioned materials are mixed, and the mixture is pressed by a hydraulic molding machine. The pressure of the molding machine is 10 MPa, and the pressurization time is 10s. It is placed in the air for natural curing for 28 days. The binder is 80% ordinary Portland cement + 10% high alumina cement + 10% lime, and the particle size of the iron ore under-sieve powder is less than 6.3mm, and the content greater than 1mm is 70%.
[0058] After curing, the compressive strength of the agglomerates is 1868N / piece, and the strength reaches the metallurgical standard YB / T005-2005 second-grade iron pellet ore standard, meeting the strength requirements for directly adding to the gasifier (>1800N / piece). It can be fed into the gasifier together with lump coal and coke through the coal spiral. Calculated by using 300 tons of agglomerates...
PUM
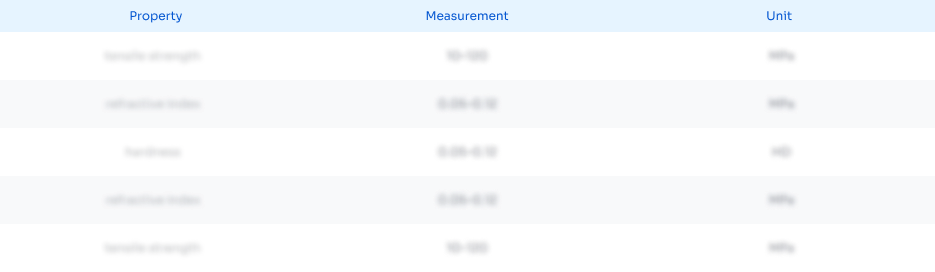
Abstract
Description
Claims
Application Information

- R&D
- Intellectual Property
- Life Sciences
- Materials
- Tech Scout
- Unparalleled Data Quality
- Higher Quality Content
- 60% Fewer Hallucinations
Browse by: Latest US Patents, China's latest patents, Technical Efficacy Thesaurus, Application Domain, Technology Topic, Popular Technical Reports.
© 2025 PatSnap. All rights reserved.Legal|Privacy policy|Modern Slavery Act Transparency Statement|Sitemap|About US| Contact US: help@patsnap.com