Wear resistant zinc alloy degassing sundries-discharging refining method
A zinc alloy and refining technology, which is applied in the field of environment-friendly wear-resistant zinc alloy degassing and impurity-removing refining, can solve the problems of less use, low inert gas refining cost, and insufficient impurity-removing effect, and achieves simple process and convenient operation. Effect
- Summary
- Abstract
- Description
- Claims
- Application Information
AI Technical Summary
Problems solved by technology
Method used
Image
Examples
Embodiment 1
[0027] The material of the wear-resistant zinc alloy casting of this embodiment is composed of the following components accounting for the total mass percentage of the alloy: 72.43% zinc, 25% aluminum, 2.5% copper, 0.02% magnesium, 0.05% cerium, and the weight of the alloy melt is 200kg .
[0028]Preheat the crucible with an intermediate frequency furnace, then add 49.44 kg of aluminum ingot and 5 kg of copper block to the crucible successively, continue to heat the crucible, and keep the temperature up to 680~690°C. When this temperature rise is reached, The aluminum ingot in the crucible is in a completely molten state, and the copper block is partially melted. 15 minutes after the aluminum ingot is melted, use a stirring rod to probe the bottom. After the copper block is not felt, that is, the copper block is completely melted, add 144.86 kg of Zinc ingots, and stop the intermediate frequency furnace to heat the crucible, and keep the aluminum and copper in the crucible ...
Embodiment 2
[0031] The material of the wear-resistant zinc alloy casting of this embodiment is composed of the following components accounting for the total mass percentage of the alloy: 71.63% zinc, 26% aluminum, 2.3% copper, 0.01% magnesium, 0.06% cerium, and the weight of the alloy melt is 200kg .
[0032] Preheat the crucible with an intermediate frequency furnace, then add 51.42 kg of aluminum ingot and 4.6 kg of copper block to the crucible successively, continue to heat the crucible, and keep the temperature up to 680~690°C. , the aluminum ingot in the crucible is in a completely molten state, and the copper block is partially melted. 15 minutes after the aluminum ingot is melted, use a stirring rod to probe the bottom. After the existence of the copper block is not felt, that is, the copper block is completely melted, then add 143.26kg Zinc ingots, and stop the intermediate frequency furnace to heat the crucible, and keep the aluminum and copper in the crucible in a molten state t...
Embodiment 3
[0035] The material of the wear-resistant zinc alloy casting of this embodiment is composed of the following components accounting for the total mass percentage of the alloy: 69.91% zinc, 28% aluminum, 2.0% copper, 0.01% magnesium, 0.08% cerium, and the weight of the alloy melt is 200kg .
[0036] Preheat the crucible with an intermediate frequency furnace, then add 55.57 kg of aluminum ingots and 4 kg of copper block to the crucible successively, continue heating the crucible, and keep the temperature up to 680~690°C. When this temperature rise is reached, The aluminum ingot in the crucible is in a completely molten state, and the copper block is partially melted. 15 minutes after the aluminum ingot is melted, use a stirring rod to probe the bottom. After the copper block is not felt, that is, the copper block is completely melted, add 139.92kg of Zinc ingots, and stop the intermediate frequency furnace to heat the crucible, and keep the aluminum and copper in the crucible...
PUM
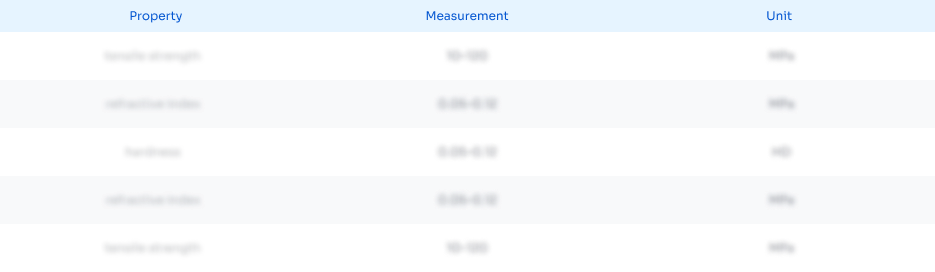
Abstract
Description
Claims
Application Information

- R&D
- Intellectual Property
- Life Sciences
- Materials
- Tech Scout
- Unparalleled Data Quality
- Higher Quality Content
- 60% Fewer Hallucinations
Browse by: Latest US Patents, China's latest patents, Technical Efficacy Thesaurus, Application Domain, Technology Topic, Popular Technical Reports.
© 2025 PatSnap. All rights reserved.Legal|Privacy policy|Modern Slavery Act Transparency Statement|Sitemap|About US| Contact US: help@patsnap.com