Rolling bearing and manufacturing method for solid lubricated rolling bearing
A rolling bearing and solid lubrication technology, applied in the direction of ball bearings, bearing components, shafts and bearings, etc., can solve the problems of bearing wear failure, bearing stuck, bearing under-lubrication, etc., to reduce manufacturing costs and maintenance costs, and improve operation reliability. the effect of prolonging the service life
- Summary
- Abstract
- Description
- Claims
- Application Information
AI Technical Summary
Problems solved by technology
Method used
Image
Examples
Embodiment 1
[0038] In this example, the thermoplastic polymer is made of polyetheretherketone (PEEK), and the solid lubricating material is made of graphite. Double-sided dust cover sealed deep groove ball bearings, such as figure 1 As shown, the bearing manufacturing process and method are as follows:
[0039] (1) Mix and homogenize granular or powder polyether ether ketone and graphite to make a mixed material;
[0040] (2) The outer ring 11, inner ring 12 and rolling elements 13 are all made of bearing steel, and are quenched and tempered according to the temperature range of the bearing, and chemical heat treatment is carried out after grinding, superfinishing and other mechanical processing. In this example In, manganese phosphating treatment is carried out;
[0041] (3) The retainer 14 is made of medium-carbon steel plate, and is subjected to manganese phosphating treatment after machining and forming;
[0042] (4) According to the current deep groove ball bearing assembly pro...
Embodiment 2
[0051] In this embodiment, the thermoplastic polymer is made of polyphenylene sulfide, and the solid lubricating material is made of molybdenum disulfide, which is made of stamped metal cage spherical roller bearings, such as figure 2 As shown, the bearing manufacturing process and method are as follows:
[0052] (1) Making granular or powdery mixed materials or composite materials of polyphenylene sulfide and molybdenum disulfide as raw materials for injection molding process;
[0053] (2) Outer ring 21, inner ring 22, spherical roller 23 and intermediate ring 25 are all made of bearing steel, and are quenched and tempered according to the temperature range of the bearing, and chemically processed after grinding and superfinishing. Heat treatment, in this example, carry out manganese series phosphating treatment;
[0054] (3) The retainer 24 is made of medium-carbon steel plate, and is subjected to manganese phosphating treatment after machining and forming;
[0055] (...
PUM
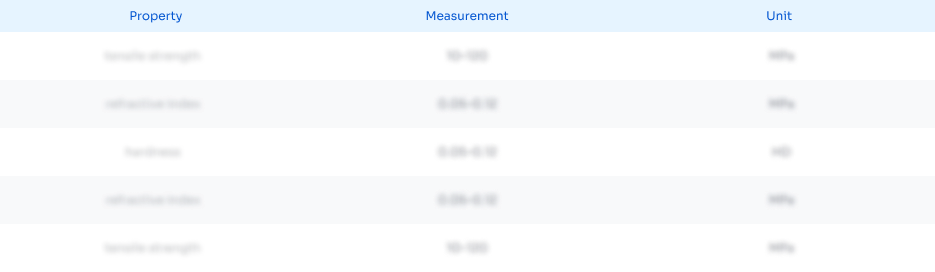
Abstract
Description
Claims
Application Information

- R&D Engineer
- R&D Manager
- IP Professional
- Industry Leading Data Capabilities
- Powerful AI technology
- Patent DNA Extraction
Browse by: Latest US Patents, China's latest patents, Technical Efficacy Thesaurus, Application Domain, Technology Topic, Popular Technical Reports.
© 2024 PatSnap. All rights reserved.Legal|Privacy policy|Modern Slavery Act Transparency Statement|Sitemap|About US| Contact US: help@patsnap.com