Dyeing process of dry spinning cakes of viscose filaments
A silk cake dyeing, viscose filament technology, applied in liquid/gas/vapor yarn/filament processing, textile material processing, removal of liquid/gas/vapor by centrifugal force, etc., can solve the waste of dye liquor and auxiliaries Sealing performance, cost and quality can not be achieved, dry silk cake swelling treatment is not enough and other problems, to achieve the effect of good sealing, cost reduction, uniform density
- Summary
- Abstract
- Description
- Claims
- Application Information
AI Technical Summary
Problems solved by technology
Method used
Image
Examples
Embodiment 1
[0037] A dry silk cake dyeing process for viscose filaments, the process steps include drying the silk cake, loading cylinder sleeves, upper creel, pre-treatment, dyeing, post-treatment and tube forming, the creel upper refers to the The cylinder cover that dry silk cake is housed is put into the yarn column on the yarn disc in the dyeing vat, and the horizontal distance between the outer sides of the dry silk cake on every two adjacent yarn columns is controlled to be 2mm; Water, the dry silk cake is completely submerged, and the silk strands are swollen, and the pressure difference between the pressure on the outside of the dry silk cake and the pressure in the cylinder liner is 0.6kg.
[0038] Swelling is completed when the pressure difference between the pressure outside the dry silk cake and the pressure inside the cylinder liner reaches 0.6kg, as long as it is greater than or equal to 0.6kg, other processes are controlled by conventional dyeing process and parameters.
Embodiment 2
[0040] A dry silk cake dyeing process for viscose filaments, the process steps include drying the silk cake, loading cylinder sleeves, upper creel, pre-treatment, dyeing, post-treatment and tube forming, the creel upper refers to the The cylinder cover that dry silk cake is housed is put into the yarn column on the yarn disc in the dyeing vat, and the horizontal distance between the outer sides of the dry silk cake on every two adjacent yarn columns is controlled to be 50mm; Water, completely immerse the dry silk cake, and carry out the swelling of the silk strands, and the pressure difference between the pressure on the outside of the dry silk cake and the pressure in the cylinder liner is at least 1.2kg.
[0041] Swelling is completed when the pressure difference between the pressure outside the dry silk cake and the pressure inside the cylinder liner reaches 0.6kg, as long as it is greater than or equal to 0.6kg, other processes are controlled by conventional dyeing process ...
Embodiment 3
[0043] A dry silk cake dyeing process for viscose filaments, the process steps include drying the silk cake, loading cylinder sleeves, upper creel, pre-treatment, dyeing, post-treatment and tube forming, the creel upper refers to the The cylinder cover that dry silk cake is housed is put into the yarn column on the yarn disc in the dyeing vat, and the horizontal distance between the outer sides of the dry silk cake on every two adjacent yarn columns is controlled to be 26mm; water, completely submerge the dry silk cake, and carry out silk swelling, and the pressure difference between the pressure on the outside of the dry silk cake and the pressure in the cylinder liner is at least 0.9kg.
[0044] Swelling is completed when the pressure difference between the pressure outside the dry silk cake and the pressure inside the cylinder liner reaches 0.6kg, as long as it is greater than or equal to 0.6kg, other processes are controlled by conventional dyeing process and parameters.
PUM
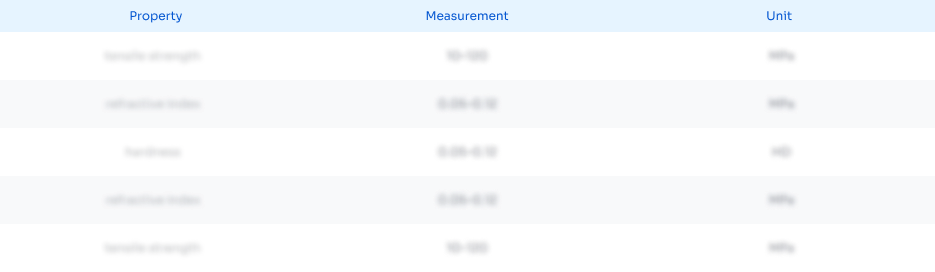
Abstract
Description
Claims
Application Information

- R&D
- Intellectual Property
- Life Sciences
- Materials
- Tech Scout
- Unparalleled Data Quality
- Higher Quality Content
- 60% Fewer Hallucinations
Browse by: Latest US Patents, China's latest patents, Technical Efficacy Thesaurus, Application Domain, Technology Topic, Popular Technical Reports.
© 2025 PatSnap. All rights reserved.Legal|Privacy policy|Modern Slavery Act Transparency Statement|Sitemap|About US| Contact US: help@patsnap.com