Antistatic material, preparation method and applications of antistatic material
An antistatic and antioxidant technology, applied in the field of polymer composite materials, can solve the problems of a large amount of solvent consumption, large addition amount, and decreased mechanical properties of materials, so as to improve dimensional stability, strength difference, and antistatic performance. Effect
- Summary
- Abstract
- Description
- Claims
- Application Information
AI Technical Summary
Problems solved by technology
Method used
Image
Examples
Embodiment 1
[0034] 70 parts of polypropylene (parts by weight, the same below), 5 parts of linear low-density polyethylene, 10 parts of EPDM, 10 parts of talcum powder above 800 mesh, 1 part of polypropylene grafted maleic anhydride, silane coupling agent 0.2 parts, 1 part of multi-walled carbon nanotubes, 2.5 parts of conductive carbon black, 0.3 parts of antioxidant 1010.
[0035] Put polypropylene, linear low-density polyethylene, elastomer, talcum powder, polypropylene grafted maleic anhydride, silane coupling agent and antioxidant 1010 into the high-speed mixer according to the above ratio and mix them for 5 minutes, then take them out in Extrude and granulate in a twin-screw extruder, the temperature of the extruder is set at 175-215°C, and the obtained pellets are made into a sample in an injection molding machine, and the temperature of the injection molding machine is set at 190-220°C. The performance test results are shown in Table 1.
Embodiment 2
[0037] 65 parts of polypropylene, 5 parts of low-density polyethylene, 5 parts of ethylene octene copolymer, 20 parts of talcum powder above 800 mesh, 1.5 parts of polypropylene grafted maleic anhydride as compatibilizer, and 0.2 parts of aluminate coupling agent , 1.5 parts of conductive carbon black, 1.5 parts of multi-walled carbon nanotubes, 0.3 parts of antioxidant 1010.
[0038] Polypropylene, linear low density polyethylene, elastomeric ethylene octene copolymer, talcum powder, compatibilizer polypropylene grafted maleic anhydride, aluminate coupling agent, multi-walled carbon nanotubes and antioxidant 1010, Put it into the high-speed mixer according to the above ratio and mix it for 5 minutes, take it out, extrude and granulate in the twin-screw extruder, set the temperature of the extruder at 175-215°C, and make the obtained pellets in the injection molding machine For the spline, the temperature of the injection molding machine was set at 190-220°C, and the performan...
Embodiment 3
[0040] 44 parts of polypropylene, 10 parts of linear low-density polyethylene, 10 parts of ethylene octene copolymer, 30 parts of talc powder with a mesh size above 800, 2 parts of grafted maleic anhydride to polypropylene, and 0.3 parts of titanate coupling agent Parts, 2 parts of multi-walled carbon nanotubes, 1.5 parts of conductive carbon black, 0.2 part of antioxidant 168;
[0041] Polypropylene, linear low density polyethylene, elastomer, talcum powder, compatibilizer polypropylene graft maleic anhydride, aluminate coupling agent, multi-walled carbon nanotubes, conductive carbon black and antioxidant 168, according to Put the above ratio into a high-speed mixer and mix for 5 minutes, take it out, extrude and pelletize in a twin-screw extruder, set the temperature of the extruder at 175-215°C, and make the pellets into samples in an injection molding machine The temperature of the injection molding machine is set at 190-220°C, and the performance test results are shown in...
PUM
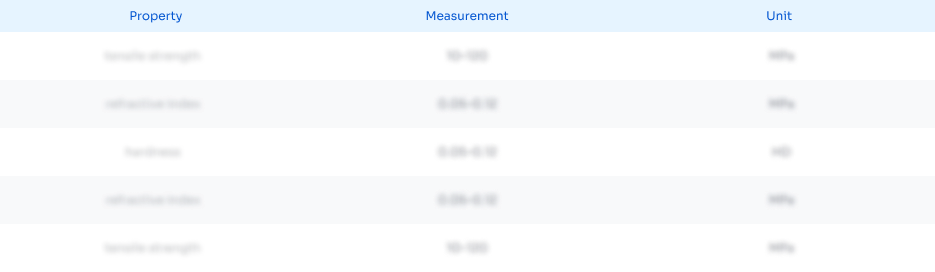
Abstract
Description
Claims
Application Information

- R&D
- Intellectual Property
- Life Sciences
- Materials
- Tech Scout
- Unparalleled Data Quality
- Higher Quality Content
- 60% Fewer Hallucinations
Browse by: Latest US Patents, China's latest patents, Technical Efficacy Thesaurus, Application Domain, Technology Topic, Popular Technical Reports.
© 2025 PatSnap. All rights reserved.Legal|Privacy policy|Modern Slavery Act Transparency Statement|Sitemap|About US| Contact US: help@patsnap.com