Centrifugal casting method of aluminum alloy impeller
An aluminum alloy impeller and centrifugal casting technology, which is applied to casting molding equipment, casting molds, and casting mold components, can solve the problems of low dimensional accuracy, poor surface quality of castings, and high production costs, and achieve high dimensional accuracy and good surface quality , the effect of high mechanical properties
- Summary
- Abstract
- Description
- Claims
- Application Information
AI Technical Summary
Problems solved by technology
Method used
Image
Examples
specific Embodiment approach 1
[0020] Specific Embodiment 1: The aluminum alloy impeller centrifugal casting method described in this embodiment is realized according to the following steps:
[0021] Step 1. Prepare the impeller wax mold: prepare the impeller wax mold according to the shape and size of the impeller, and then sand and dewax the impeller wax mold to obtain the impeller shell;
[0022] Step 2. Wax mold preheating: put the impeller shell obtained in step 1 into a resistance furnace for preheating, the preheating temperature is 400-500°C, and the preheating time is 2-4 hours;
[0023] Step 3. Tool treatment: Brush the surface of the tool in contact with the molten aluminum during casting and smelting with a water-based paint. The above-mentioned water-based paint is a solution of zinc oxide, talcum powder and water glass, and then put the above-mentioned tools into a resistance furnace for drying. The temperature is 300-400°C, and the drying time is 2-4 hours;
[0024] Step 4, using Al7Si alumi...
specific Embodiment approach 2
[0031] Embodiment 2: The preheating temperature in step 2 of this embodiment is 450°C. Others are the same as in the first embodiment.
specific Embodiment approach 3
[0032] Embodiment 3: The preheating time in step 2 of this embodiment is 2 to 4 hours. Others are the same as in the first or second embodiment.
PUM
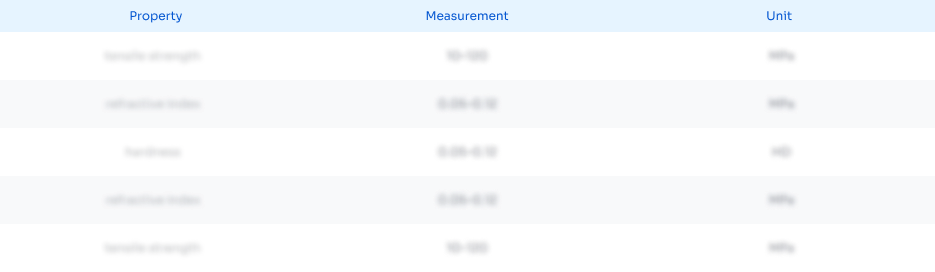
Abstract
Description
Claims
Application Information

- R&D Engineer
- R&D Manager
- IP Professional
- Industry Leading Data Capabilities
- Powerful AI technology
- Patent DNA Extraction
Browse by: Latest US Patents, China's latest patents, Technical Efficacy Thesaurus, Application Domain, Technology Topic, Popular Technical Reports.
© 2024 PatSnap. All rights reserved.Legal|Privacy policy|Modern Slavery Act Transparency Statement|Sitemap|About US| Contact US: help@patsnap.com