Centrifugal casting method for flange casting with bolt holes
A technology of centrifugal casting and centrifugal casting machine, which is applied in the field of casting, and can solve problems such as the inability to effectively guarantee the accuracy of bolt holes, many casting processes, and high scrap rate, and achieve the effects of high raw material utilization, excellent overall performance, and low cost
- Summary
- Abstract
- Description
- Claims
- Application Information
AI Technical Summary
Problems solved by technology
Method used
Examples
Embodiment
[0012] (1) Smelting: put the selected raw materials into the electric furnace for smelting, wait until the raw materials are melted into molten metal, carry out composition testing on the molten metal, and add enough missing elements to the molten metal according to the test results to meet the chemical composition requirements of the material, and then continue Heating to make the molten metal temperature reach 1700°C;
[0013] (2) Casting mold preparation, the mold adopts a metal mold with bolt hole patterns on the mold;
[0014] (3) Casting molding: Preheat the casting mold to 850°C to keep a constant temperature, start the centrifugal casting machine, drive the casting mold installed on the centrifugal casting machine to rotate, pour the molten metal into the casting mold, and cast it;
[0015] (4) Shut down the casting to take out the mold: After the casting is naturally cooled to 800 ° C for 15 minutes, stop the machine and take off the casting mold, cool it to room temp...
PUM
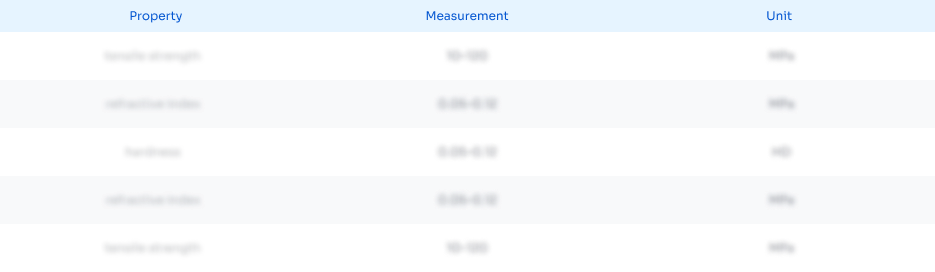
Abstract
Description
Claims
Application Information

- R&D Engineer
- R&D Manager
- IP Professional
- Industry Leading Data Capabilities
- Powerful AI technology
- Patent DNA Extraction
Browse by: Latest US Patents, China's latest patents, Technical Efficacy Thesaurus, Application Domain, Technology Topic, Popular Technical Reports.
© 2024 PatSnap. All rights reserved.Legal|Privacy policy|Modern Slavery Act Transparency Statement|Sitemap|About US| Contact US: help@patsnap.com