Method for producing high carbon steel through double-slag high drawing carbon tapping
A high-carbon steel and high-draw carbon technology is applied in the field of high-carbon steel production by double-slag method high-draw carbon tapping, which can solve the problems of serious phosphorus reversion and low production efficiency, and achieves improved furnace age, reduced bottom blowing flow, The effect of improving the dephosphorization ability
- Summary
- Abstract
- Description
- Claims
- Application Information
AI Technical Summary
Problems solved by technology
Method used
Examples
Embodiment 1
[0029] According to the method for producing high-carbon steel by double slag method high-drawing carbon tapping of the present invention, 185 tons of molten iron and 23.5 tons of scrap steel are added to a 210-ton converter, and the conditions of the molten iron are: 4.13%C, 0.37%Si, 0.23%Mn , 0.10%P, 0.038%S, 1357℃; the first stage uses 2.8Nm 3 / min / t oxygen supply intensity blowing, the position of the blowing gun is 2.5 meters, the position of the process gun is 2.7-2.1 meters, and the position of the carbon pulling gun is 1.9 meters. After the blowing is started, 5 tons of lime (25 kg / tons of steel), 1.5 tons of ore (7 kg / ton of steel), the bottom blowing nitrogen flow rate is 0.1Nm 3 / min / t, the composition and temperature of molten iron at the end of the first stage are: 3.53%C, 0.002%Si, 0.09%Mn, 0.021%P, 0.041%S, 1387℃; the second stage uses 3.3Nm 3 / min / t oxygen supply intensity blowing, the blowing gun position is 2.3 meters, the process gun position is 2.6-2.1 me...
Embodiment 2
[0031] According to the method for producing high-carbon steel by double-slag method high-drawing carbon tapping of the present invention, add 183 tons of molten iron and 25 tons of scrap steel into a 210-ton converter, and the conditions of the molten iron are: 4.03%C, 0.58%Si, 0.21%Mn , 0.097%P, 0.034%S, 1377℃; the first stage uses 2.8Nm 3 / min / t of oxygen supply intensity blowing, the position of the blowing gun is 2.4 meters, the position of the process gun is 2.6-2.1 meters, the position of the carbon pulling gun is 1.8 meters, and 4.5 tons of lime (23 kg / tons of steel), 1.5 tons of ore (7 kg / ton of steel), the bottom blowing nitrogen flow rate is 0.1Nm 3 / min / t, the composition and temperature of molten iron at the end of the first stage are: 3.68%C, 0.002%Si, 0.08%Mn, 0.023%P, 0.035%S, 1369℃; the second stage uses 3.3Nm 3 / min / t oxygen supply intensity blowing, the blowing gun position is 2.3 meters, the process gun position is 2.7-2.0 meters, the blowing gun position...
PUM
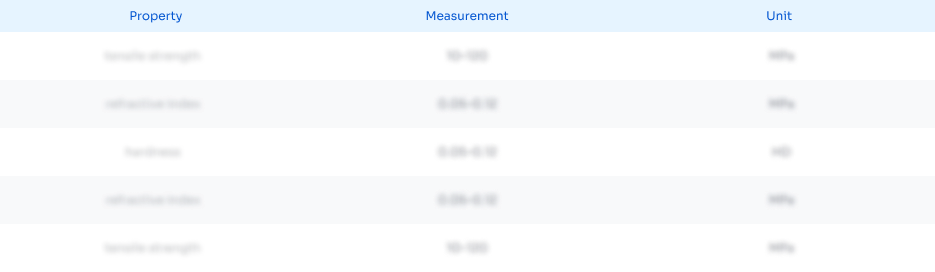
Abstract
Description
Claims
Application Information

- R&D
- Intellectual Property
- Life Sciences
- Materials
- Tech Scout
- Unparalleled Data Quality
- Higher Quality Content
- 60% Fewer Hallucinations
Browse by: Latest US Patents, China's latest patents, Technical Efficacy Thesaurus, Application Domain, Technology Topic, Popular Technical Reports.
© 2025 PatSnap. All rights reserved.Legal|Privacy policy|Modern Slavery Act Transparency Statement|Sitemap|About US| Contact US: help@patsnap.com