Converter smelting method for improving end molten steel remainder Mn with medium-high-Mn, high-P and low-Si molten iron
A converter smelting, high-phosphorus technology, applied in the field of medium-high-manganese, high-phosphorus, low-silicon molten iron to increase residual manganese in molten steel at the end point, and in the field of converter smelting, to reduce the amount of addition, improve the dephosphorization effect of smelting slag, and reduce the effect of returning phosphorus to molten steel
- Summary
- Abstract
- Description
- Claims
- Application Information
AI Technical Summary
Problems solved by technology
Method used
Examples
Embodiment 1
[0033] A. Smelting and loading process: after the steel tapping and slag splashing of the upper furnace, all the final slag is kept in the converter, according to 4.0kg / t 钢 The amount, add conventional active lime to the converter; according to 55kg / t 钢 The ratio of steel scrap is loaded into a 50-ton LD converter with the following mass ratios of steel scrap: C 0.20wt%, Si 0.35wt%, Mn 1.20wt%, P 0.035wt%, S 0.028wt%, the rest is Fe and unavoidable impurity; according to 50kg / t 钢 The proportion of pig iron loaded into the 50-ton LD converter is added with the following mass ratios of pig iron: C 3.3wt%, Si 0.30 wt%, Mn 0.32wt%, P 0.058wt%, S 0.018wt%, the rest is Fe and unavoidable impurity) into the LD converter; then press 980kg / t 钢 The proportion of molten iron is loaded, and the following temperature and mass ratio of medium-high manganese, high-phosphorus and low-silicon molten iron are added to a 50-ton LD converter: molten iron temperature 1300 ° C, molten iron compos...
Embodiment 2
[0039] A. Smelting and loading process: after the steel tapping and slag splashing of the upper furnace, all the final slag is kept in the converter, according to 4.5kg / t 钢 The amount, add conventional active lime to the converter; according to 82kg / t 钢 The proportion of steel scrap loaded into the 50-ton LD converter is added with the following mass ratio of steel scrap: C 0.23wt%, Si 0.42wt%, Mn 1.30wt%, P 0.040wt%, S 0.033wt%, the rest is Fe and unavoidable impurity; according to 50kg / t 钢The proportion of pig iron loaded into the 50-ton LD converter is added with the following mass ratio of pig iron: C 3.5wt%, Si 0.40 wt%, Mn 0.43wt%, P 0.067wt%, S 0.022wt%, the rest is Fe and unavoidable impurity) into the LD converter; then press 965kg / t 钢 The proportion of molten iron is loaded, and the following temperature and mass ratio of medium-high manganese, high-phosphorus and low-silicon molten iron are added to a 50-ton LD converter: molten iron temperature 1320 ° C, molten i...
Embodiment 3
[0045] A. Smelting and loading process: after the steel tapping and slag splashing of the upper furnace, all the final slag is kept in the converter, at a rate of 5.0kg / t 钢 The amount, add conventional active lime to the converter; according to 70kg / t 钢 The proportion of scrap steel is loaded into the 50-ton LD converter with the following mass ratio of scrap steel: C 0.26wt%, Si 0.50wt%, Mn 1.40wt%, P 0.046wt%, S 0.039wt%, the rest is Fe and unavoidable impurity; according to 50kg / t 钢 The proportion of pig iron loaded into the 50-ton LD converter is added with the following mass ratio of pig iron: C 3.6wt%, Si 0.50wt%, Mn 0.55wt%, P 0.075wt%, S 0.027wt%, the rest is Fe and unavoidable impurity) into the LD converter; then press 950kg / t 钢 The molten iron is loaded into the ratio, and the following temperature and mass ratio of medium-high manganese, high-phosphorus and low-silicon molten iron are added to a 50-ton LD converter: molten iron temperature 1330 ° C, molten iron c...
PUM
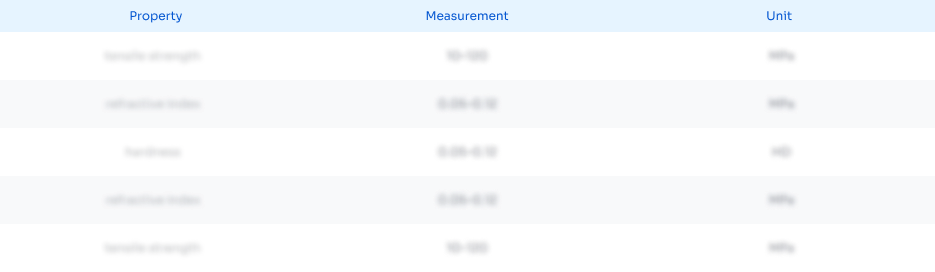
Abstract
Description
Claims
Application Information

- Generate Ideas
- Intellectual Property
- Life Sciences
- Materials
- Tech Scout
- Unparalleled Data Quality
- Higher Quality Content
- 60% Fewer Hallucinations
Browse by: Latest US Patents, China's latest patents, Technical Efficacy Thesaurus, Application Domain, Technology Topic, Popular Technical Reports.
© 2025 PatSnap. All rights reserved.Legal|Privacy policy|Modern Slavery Act Transparency Statement|Sitemap|About US| Contact US: help@patsnap.com