A preparation method for extracting carbon and preserving manganese by converting high-manganese, high-silicon, and high-phosphorus iron into hot water
A converter smelting and molten iron technology, which is applied in the direction of manufacturing converters and improving process efficiency, can solve the problem of no relevant research reports on the smelting process of carbon extraction and manganese preservation, and achieves the improvement of smelting technical and economic indicators, and good smelting slag. Effects of dephosphorization, optimized kinetic and thermodynamic conditions
- Summary
- Abstract
- Description
- Claims
- Application Information
AI Technical Summary
Problems solved by technology
Method used
Examples
preparation example Construction
[0016] The preparation method of converter smelting high-manganese, high-silicon, high-phosphorus hot metal to extract carbon and preserve manganese in the present invention comprises the following process steps:
[0017] A. Smelting and loading process: pour out all the final slag in the converter after tapping the steel in the upper furnace and splashing the slag, according to 130-150kg / t 钢 The scrap steel is put into the ratio, and the scrap steel is added to the 50-ton LD converter; according to 920-940kg / t 钢 The molten iron is loaded into the ratio, and the following temperature and mass ratio of high-manganese, high-silicon, and high-phosphorus molten iron are added to a 50-ton LD converter: molten iron temperature ≥ 1290 ° C, molten iron composition C 4.5-5.2wt%, Si 0.70-1.00wt%, Mn 1.10-1.50wt%, P 0.120-0.170wt%, S≤0.035wt%, the rest is Fe and unavoidable impurities;
[0018] B. Pre-smelting process: In step A, after the high-manganese, high-silicon, high-phosphorus m...
Embodiment 1
[0029] A. Smelting and loading process: pour out all the final slag in the converter after tapping the steel in the upper furnace and splashing the slag, according to 130kg / t 钢 The proportion of scrap steel is loaded into the 50-ton LD converter with the following mass ratio of scrap steel: C 0.17wt%, Si 0.40wt%, Mn 1.25wt%, P 0.036wt%, S0.035wt%, the rest is Fe and unavoidable impurity; according to 940kg / t 钢 The molten iron is loaded into the ratio, and the following temperature and mass ratio of high-manganese, high-silicon, and high-phosphorus molten iron are added to a 50-ton LD converter: molten iron temperature 1290 ° C, molten iron composition C4.5wt%, Si 0.70wt%, Mn 1.10wt%, P 0.120wt%, S 0.020wt%, the rest is Fe and unavoidable impurities.
[0030] B. Pre-smelting process: In step A, after the high-manganese, high-silicon, high-phosphorus molten iron and steel scrap cold material are loaded into a 50-ton LD converter, the front and rear shaking furnaces expose the m...
Embodiment 2
[0035] A. Smelting and loading process: pour out all the final slag in the converter after tapping the steel in the upper furnace and splashing the slag, according to 140kg / t 钢 The ratio of steel scrap is loaded into a 50-ton LD converter with the following mass ratios: C 0.20wt%, Si 0.50wt%, Mn 1.38wt%, P 0.042wt%, S 0.040wt%, the rest is Fe and unavoidable impurity; according to 930kg / t 钢 The molten iron is loaded into the ratio, and the following temperature and mass ratio of high-manganese, high-silicon, and high-phosphorus molten iron are added to a 50-ton LD converter: molten iron temperature 1300 ° C, molten iron composition C4.9wt%, Si 0.85wt%, Mn 1.30wt%, P 0.145wt%, S0.030wt%, the rest is Fe and unavoidable impurities.
[0036] B. Pre-smelting process: In step A, after the high-manganese, high-silicon, high-phosphorus molten iron and steel scrap cold material are loaded into a 50-ton LD converter, the front and rear shaking furnaces expose the molten iron, and then ...
PUM
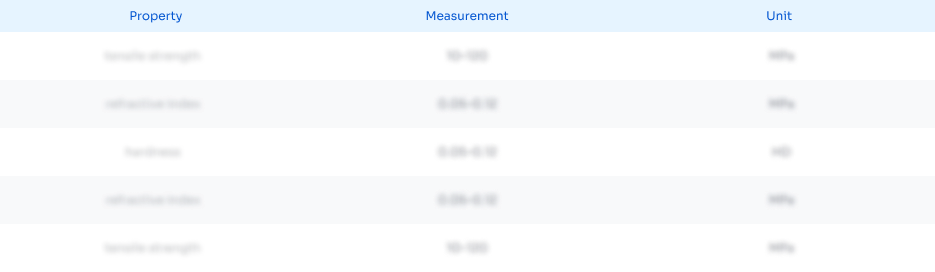
Abstract
Description
Claims
Application Information

- Generate Ideas
- Intellectual Property
- Life Sciences
- Materials
- Tech Scout
- Unparalleled Data Quality
- Higher Quality Content
- 60% Fewer Hallucinations
Browse by: Latest US Patents, China's latest patents, Technical Efficacy Thesaurus, Application Domain, Technology Topic, Popular Technical Reports.
© 2025 PatSnap. All rights reserved.Legal|Privacy policy|Modern Slavery Act Transparency Statement|Sitemap|About US| Contact US: help@patsnap.com