Method for welding copper oxygen lance end for steelmaking with steel pipe sub
A welding method and a technology of copper ends, which are applied in the field of workpiece welding, can solve the problems of low weld strength, large residual stress, and large difference in thermal conductivity, etc., and achieve the effects of ensuring welding quality, eliminating residual stress, and improving weld strength
- Summary
- Abstract
- Description
- Claims
- Application Information
AI Technical Summary
Problems solved by technology
Method used
Image
Examples
Embodiment Construction
[0015] The copper end of the oxygen lance used in steelmaking is made of pure copper, and the steel pipe nipple (including the inner pipe and outer pipe) is made of No. 20 steel. The melting point temperature difference between the two materials is about 400°C, and the mechanical properties are also very different. The purpose of preheating before welding is to improve the molecular activity, so that the alloy phase region of the transition layer can be formed as wide as possible after welding, so as to improve the mechanical properties of the weld. From the perspective of production cost and operability, it is impossible to obtain different preheating temperatures for two workpieces by preheating in an ordinary electric furnace, while using the same preheating temperature cannot take into account the optimum conditions for both copper and steel materials. Optimum preheating temperature zone. In addition, according to the ordinary heating process, the heating time of the workp...
PUM
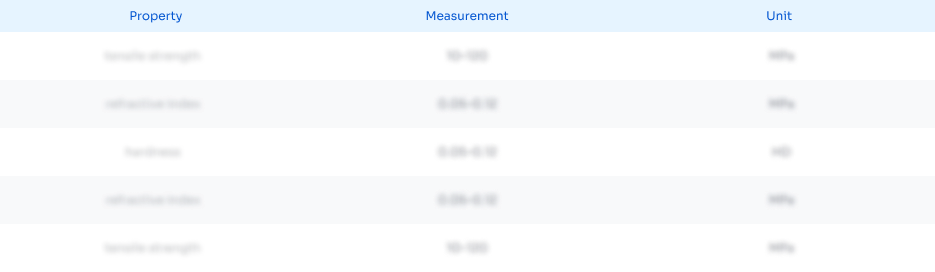
Abstract
Description
Claims
Application Information

- R&D Engineer
- R&D Manager
- IP Professional
- Industry Leading Data Capabilities
- Powerful AI technology
- Patent DNA Extraction
Browse by: Latest US Patents, China's latest patents, Technical Efficacy Thesaurus, Application Domain, Technology Topic, Popular Technical Reports.
© 2024 PatSnap. All rights reserved.Legal|Privacy policy|Modern Slavery Act Transparency Statement|Sitemap|About US| Contact US: help@patsnap.com