Cooling system for rolled stripe continuously-casting production line and control method thereof
A cooling system and production line technology, applied in metal rolling, temperature control, metal rolling, etc., can solve the problems of high manufacturing cost and maintenance cost, design, cooling, etc., achieve uniform rolling structure and performance, simple and flexible device , the effect of high control precision
- Summary
- Abstract
- Description
- Claims
- Application Information
AI Technical Summary
Problems solved by technology
Method used
Image
Examples
Embodiment
[0137] The main parameters of a specific embodiment of the strip continuous casting line cooling system after rolling of the present invention are as follows:
[0138] 1. The total length of the cooling zone is 8360mm, and three header areas are designed, namely, the first header area 5, the second header area 6 and the third header area 7, such as figure 1 shown.
[0139] 2. The diameter of the upper nozzle in the first header area 5 is designed to be 22mm, the height is 1700mm, the header spacing is designed to be 380mm, the number of headers is 5, and the number of nozzles on each header is 26, double rows, that is, the total 52, in a dislocation arrangement, such as figure 2 shown.
[0140] 3. The diameter of the lower nozzles in the first header area 5 is designed to be 14.3mm, the header spacing is designed to be 380mm, the height is 120mm, the number of headers is 10, and the number of nozzles on each header is 42, single row, in the form of Misalignment, such as ...
PUM
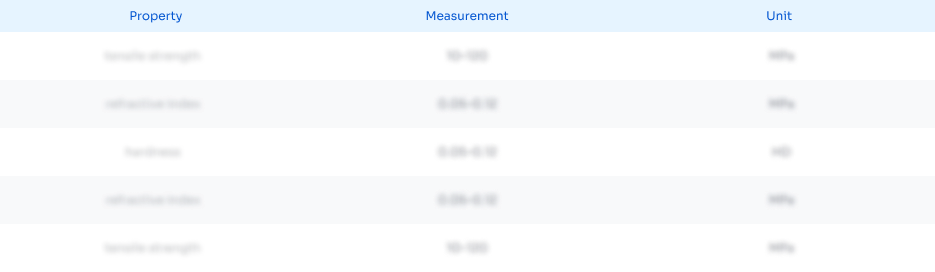
Abstract
Description
Claims
Application Information

- Generate Ideas
- Intellectual Property
- Life Sciences
- Materials
- Tech Scout
- Unparalleled Data Quality
- Higher Quality Content
- 60% Fewer Hallucinations
Browse by: Latest US Patents, China's latest patents, Technical Efficacy Thesaurus, Application Domain, Technology Topic, Popular Technical Reports.
© 2025 PatSnap. All rights reserved.Legal|Privacy policy|Modern Slavery Act Transparency Statement|Sitemap|About US| Contact US: help@patsnap.com