Preparation method of catalyst for synthesizing methacrylic acid
A methacrylic acid and catalyst technology, which is applied in the preparation of organic compounds, the preparation of carboxylate, chemical instruments and methods, etc., can solve the problems of difficult industrial application, shortened service life of catalysts, and expensive ceramic whiskers.
- Summary
- Abstract
- Description
- Claims
- Application Information
AI Technical Summary
Problems solved by technology
Method used
Image
Examples
Embodiment 1
[0018] Add 158.334 grams of molybdenum trioxide and 9.1 grams of vanadium pentoxide into 1500 grams of distilled water, heat to 80°C and stir for 2 hours, then add 86.47 grams of 17% phosphoric acid, and reflux for 36 hours under stirring to obtain solution A. Dissolve 8.768 grams of 1-butyl-3-methylimidazole in 300 grams of distilled water to obtain solution B, add B to A under stirring at 60°C, and age at a constant temperature for 2 hours, take 19.491 grams of cesium nitrate, nitric acid trihydrate 7.248 grams of copper, 12.12 grams of ferric nitrate nonahydrate, and 4.3425 grams of cerium nitrate hexahydrate were dissolved in 700 grams of distilled water to obtain solution C. Under stirring at 60 ° C, C was added to the mixed solution formed by B and A, and aged at a constant temperature for 6 hours , then evaporate the water to concentrate the slurry to obtain a solid, dry it at 110°C for 12 hours, press it into a cylinder with a diameter of 5mm and a height of 4.5mm, calc...
Embodiment 2
[0024] Add 158.334 grams of molybdenum trioxide and 11.698 grams of ammonium metavanadate into 1500 grams of distilled water, heat to 80°C and stir for 2 hours, then add 69.176 grams of 17% phosphoric acid, and reflux for 6 hours under stirring to obtain solution A. Dissolve 4.384 grams of 1-butyl-3-methylimidazole in 300 grams of distilled water to obtain solution B, add B to A under stirring at 60°C, and age at a constant temperature for 2 hours, take 19.491 grams of cesium nitrate, nitric acid trihydrate 12.08 grams of copper, 8.08 grams of iron nitrate nonahydrate, and 4.3425 grams of cerium nitrate hexahydrate were dissolved in 700 grams of distilled water to obtain solution C. Under stirring at 60 ° C, C was added to the mixed solution formed by B and A, and aged at constant temperature for 6 hours , then evaporate the water to concentrate the slurry to obtain a solid, dry it at 110°C for 12 hours, press it into a cylinder with a diameter of 5mm and a height of 4.5mm, cal...
Embodiment 3
[0036] Except that 4.024 g of 1-butyl-3-methylimidazole nitrate was used to replace 4.384 g of 1-butyl-3-methylimidazole bromide when preparing solution B, other preparation steps were the same as in Example 2.
[0037] Under the same conditions as in Example 1, the catalyst was used for the gas-phase oxidation of methacrolein to methacrylic acid, and the results are listed in Table 1.
PUM
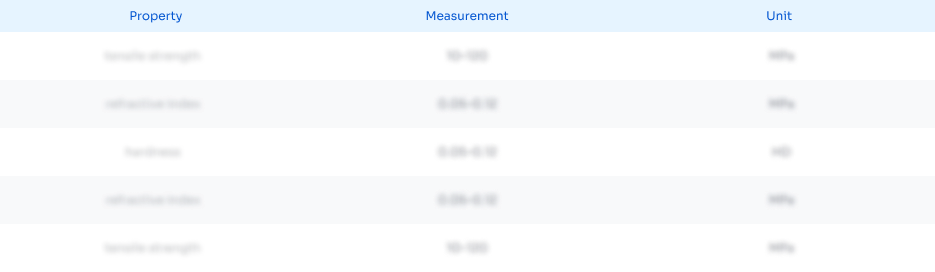
Abstract
Description
Claims
Application Information

- R&D
- Intellectual Property
- Life Sciences
- Materials
- Tech Scout
- Unparalleled Data Quality
- Higher Quality Content
- 60% Fewer Hallucinations
Browse by: Latest US Patents, China's latest patents, Technical Efficacy Thesaurus, Application Domain, Technology Topic, Popular Technical Reports.
© 2025 PatSnap. All rights reserved.Legal|Privacy policy|Modern Slavery Act Transparency Statement|Sitemap|About US| Contact US: help@patsnap.com