Method for producing iron pellet with sulfur acid residue containing large contents of impurities and enriching valuable metal
A technology for valuable metals and sulfuric acid slag, which is applied in the field of producing iron pellets and enriching valuable metals. It can solve the problems that affect the full utilization of high-impurity sulfuric acid slag, limit the comprehensive utilization of sulfuric acid slag and iron resources, and improve metal recovery. efficiency, avoiding the effect of oxidizing atmosphere
- Summary
- Abstract
- Description
- Claims
- Application Information
AI Technical Summary
Problems solved by technology
Method used
Image
Examples
Embodiment 1
[0041] Using the sulfuric acid slag shown in Table 1 as the raw material, add 6% reducing agent to the sulfuric acid slag, including 4% lignite and 2% coke powder. The length-to-diameter ratio of the kiln is 12; the inclination is 4%; the rotation speed is 0.8 r / min, the temperature of the kiln head is controlled at 800-850°C, the temperature of the kiln tail is 400-450°C, and the kiln is fired in a weak reducing atmosphere for 90 minutes. After the calcined sand leaves the kiln, it is directly sent to the cylindrical mixer, and 3% ferrous chloride and 2.5% sodium-based bentonite are added by the weight of the calcined sand, both of which are diluted with water and then added, and then added with 2% lignite and 1% coke powder , and control the moisture content of the material at 11~12%. After fully stirring and mixing in the mixer, send it to the disc granulator to make pellets with a particle size of 20~30mm, and then send it to the chain machine at a temperature of 400~1000°C...
Embodiment 2
[0043] Using the sulfuric acid slag shown in Table 1 as the raw material, add 9% reducing agent to the sulfuric acid slag, including 4% lignite and 5% coke powder, and control the basicity of the ingredients to 0.67. The length-to-diameter ratio of the kiln is 15; the inclination is 5%; the rotation speed is 1.2 r / min. The temperature of the kiln head is controlled at 850-900°C, the temperature of the kiln tail is 450-500°C, and the kiln is fired in a weak reducing atmosphere for 80 minutes. After the calcined sand leaves the kiln, it is directly sent to the cylinder mixer, and 4% ferrous chloride and 1.5% calcium-based bentonite are added by the weight of the calcined sand, both of which are diluted with water and then added, and then 3% lignite is added, and the moisture content of the material is controlled. 11~12%, fully stirred and mixed in the mixer, then sent to the pan granulator to make pellets with a particle size of 20~30mm, and then sent to the chain dryer for casca...
Embodiment 3
[0045] Using the sulfuric acid slag shown in Table 1 as the raw material, add 7% reducing agent to the sulfuric acid slag, including 1% lignite and 6% coke powder, and control the basicity of the ingredients to 0.6. The length-to-diameter ratio of the kiln is 12; the inclination is 6%; the rotation speed is 1.1 r / min, the temperature of the kiln head is controlled at 750-800°C, the temperature of the kiln tail is 350-400°C, and the kiln is fired in a weak reducing atmosphere for 100min. After the calcined sand leaves the kiln, it is directly sent to the cylinder mixer, and 5% ferrous chloride and 3% sodium bentonite are added by the weight of the calcined sand, both of which are diluted with water and then added, and then added with 1% lignite and 3% coke powder , and control the moisture content of the material at 11~12%, fully stir and mix in the mixer, and then send it to the pan granulator, use the pan granulator to make pellets with a particle size of 20~30mm, and then sen...
PUM
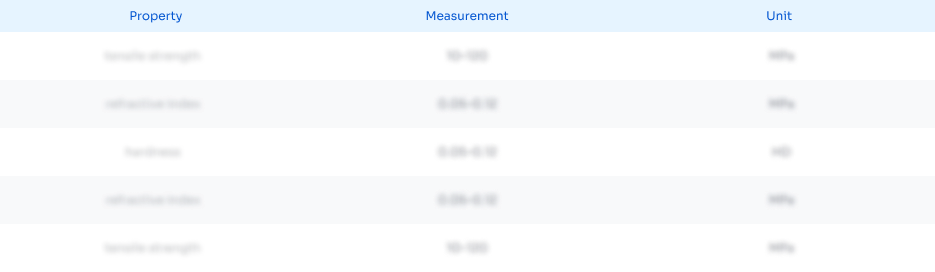
Abstract
Description
Claims
Application Information

- R&D
- Intellectual Property
- Life Sciences
- Materials
- Tech Scout
- Unparalleled Data Quality
- Higher Quality Content
- 60% Fewer Hallucinations
Browse by: Latest US Patents, China's latest patents, Technical Efficacy Thesaurus, Application Domain, Technology Topic, Popular Technical Reports.
© 2025 PatSnap. All rights reserved.Legal|Privacy policy|Modern Slavery Act Transparency Statement|Sitemap|About US| Contact US: help@patsnap.com