Natural fiber filled polyethylene composite material and preparation method thereof
A technology of natural fibers and composite materials, applied in the field of polymer composite material preparation, can solve problems such as poor mechanical properties, and achieve the effects of excellent mechanical properties, good adjustability and good processing performance.
- Summary
- Abstract
- Description
- Claims
- Application Information
AI Technical Summary
Problems solved by technology
Method used
Image
Examples
preparation example Construction
[0038] The present invention also proposes a method for preparing a natural fiber-filled polyethylene composite material, said method comprising the following steps:
[0039] Step 1: Measure the weight of the natural fiber powder, put it into a high-speed mixer, and stir at a speed of 2000r / min for 20-30 minutes;
[0040] Step 2: Add other ingredients in proportion, mix with each other for 10-20 minutes, and then put them into the co-rotating parallel twin-screw extruder;
[0041] Step 3: Carry out granulation, and extrude from the co-rotating parallel twin-screw extruder to obtain a natural fiber-filled polyethylene composite material.
[0042] The material obtained in step 3 is pellets.
[0043] The range of the stirring temperature T1 in the step 1 is: 100°C≤T1≤120°C.
[0044] The range of the granulation temperature T2 in the step 3 is: 160°C≤T2≤180°C.
Embodiment 1
[0046] Step 1: measure, put the measured natural natural fiber powder wood powder (80 mesh) into a high-speed mixer, heat to 100-120°C, and stir at 2000r / min for 20-30 minutes;
[0047] Step 2: Add high-density high-density polyethylene (MI=3), calcium carbonate, stearic acid-PEI condensate in proportion Zinc stearate and EBSwax, the preferred dosage is respectively 30% by weight, 6% by weight, 1.5% by weight, 1.5% by weight and 1% by weight, both mixing and stirring each other for 10-20 minutes, mixing The finished product after mixing is put into the co-rotating parallel twin-screw extruder;
[0048] Step 3: Carrying out granulation, the required temperature at this time is 160-180° C., and the granules of the natural fiber-filled polyethylene composite material are obtained under this temperature condition.
[0049] The pellets obtained in the step 3 are extruded by a conical screw, and can be made into profiled parts of various shapes.
Embodiment 2
[0051] Step 1: measure, put the measured natural natural fiber powder bamboo powder (100 mesh) into a high-speed mixer, heat to 100-120 ° C and stir at a speed of 2000 r / min for 20-30 minutes;
[0052] Step 2: Add high-density high-density polyethylene (MI=5), talcum powder, and lauric acid-PEI condensate in proportion Zinc stearate and EBSwax, described preferred consumption is respectively 25% weight ratio, 5% weight ratio, 2.5% weight ratio, 1.5% and weight ratio 1% weight ratio, promptly mixed each other and stirred 10-20 minute, mixed The finished product after mixing is put into the co-rotating parallel twin-screw extruder;
[0053] Step 3: Carrying out granulation, the required temperature at this time is 160-180° C., and the granules of the natural fiber-filled polyethylene composite material are obtained under this temperature condition.
[0054] The pellets obtained in the step 3 are extruded by a conical screw, and can be made into profiled parts of various shapes...
PUM
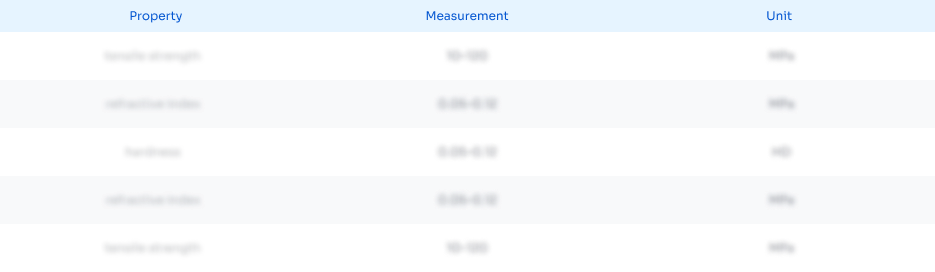
Abstract
Description
Claims
Application Information

- R&D
- Intellectual Property
- Life Sciences
- Materials
- Tech Scout
- Unparalleled Data Quality
- Higher Quality Content
- 60% Fewer Hallucinations
Browse by: Latest US Patents, China's latest patents, Technical Efficacy Thesaurus, Application Domain, Technology Topic, Popular Technical Reports.
© 2025 PatSnap. All rights reserved.Legal|Privacy policy|Modern Slavery Act Transparency Statement|Sitemap|About US| Contact US: help@patsnap.com