Power generation method, and device for gasified production of energy products and thermal power generation
A technology for producing energy and products, which is applied in the field of gasification to produce energy products and thermal power generation devices, can solve problems such as insufficient utilization of system energy, and achieve the effect of improving energy utilization efficiency and power generation efficiency
- Summary
- Abstract
- Description
- Claims
- Application Information
AI Technical Summary
Problems solved by technology
Method used
Image
Examples
Embodiment 1
[0052] see figure 1 , taking the catalytic gasification of bituminous coal and supercritical water with water as the working medium for power generation as an example. Coal is crushed and ground to make coal powder with a particle size of less than 150 microns, and the catalyst Na 2 CO 3 (consumption amount is 10% of coal powder mass) and water to prepare coal water slurry with coal powder dry base concentration of 40%. The coal-water slurry is pressurized, preheated to 23MPa, and enters the reactor at 550°C (the reactor is a gasifier in this embodiment), and oxygen is introduced into the gasifier at the same time (the gasification agent in this embodiment is oxygen ). Part of the coal-water slurry reacts with the added oxygen in the gasifier, raising the temperature to 650°C. In a supercritical state, coal and water react under the action of a catalyst to generate a mixed gas rich in methane. The main components of the mixed gas are methane, carbon monoxide, carbon diox...
Embodiment 2
[0054] also refer to figure 2 , using water as the working medium for power generation, taking the supercritical water gasification of bituminous coal as an example. The bituminous coal is ground into a 50% coal-water slurry by a wet grinder, and then sent to the gasifier (the reactor in this embodiment is a gasifier) through a pump under pressure. At the same time, oxygen or air is fed into the gasification furnace as a gasification agent. The operating temperature of the gasification furnace is about 750° C. and the operating pressure is 27.0 MPa. Coal reacts with the above-mentioned gasifying agent at high temperature to generate gas rich in carbon monoxide, hydrogen, carbon dioxide, and methane. The post-reaction mixture exiting the gasifier includes coal gas, tar and unreacted gasification agent. The reacted mixture is exchanged with 23MPa water from the booster pump in the second heat exchanger, and the pressurized water is turned into high-temperature and high-pres...
Embodiment 3
[0056] see figure 2 , using water as the working medium for power generation, taking the catalytic gasification of lignite and supercritical water as an example. The coal is prepared into a coal water slurry with a particle size of less than 150 microns through a wet mill, the concentration of the coal water slurry is 35%, and the coal water slurry contains catalyst K 2 CO 3 (The amount is 3% of the pulverized coal quality). The coal-water slurry is pressurized, preheated to 35MPa, and enters the gasifier at 450°C (the reactor in this embodiment is a gasifier), and oxygen is introduced into the gasifier at the same time. Part of the coal-water slurry reacts with the added oxygen in the gasifier, raising the temperature to 570°C. In a supercritical state, coal and water react under the action of a catalyst to generate a mixed gas rich in methane. The main components of the mixed gas are methane, carbon monoxide, carbon dioxide, hydrogen and so on. The gasifier products in...
PUM
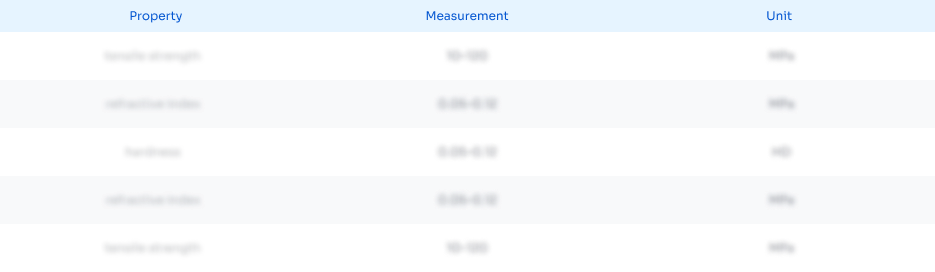
Abstract
Description
Claims
Application Information

- Generate Ideas
- Intellectual Property
- Life Sciences
- Materials
- Tech Scout
- Unparalleled Data Quality
- Higher Quality Content
- 60% Fewer Hallucinations
Browse by: Latest US Patents, China's latest patents, Technical Efficacy Thesaurus, Application Domain, Technology Topic, Popular Technical Reports.
© 2025 PatSnap. All rights reserved.Legal|Privacy policy|Modern Slavery Act Transparency Statement|Sitemap|About US| Contact US: help@patsnap.com