Method for manufacturing porous polishing and grinding tool
A technology of tool and micropowder, which is applied in the field of preparation of porous nickel-based polishing tools, can solve the problems of difficult control of pore size and porosity, and achieve the effects of increased polishing removal rate, reduced polishing consumption, and stable and reliable quality
- Summary
- Abstract
- Description
- Claims
- Application Information
AI Technical Summary
Problems solved by technology
Method used
Image
Examples
Embodiment 1
[0026] Disperse 20 grams of 1 mm micronized diamond in one liter of ethanol, add 1 gram of sodium dodecylbenzenesulfonate, and ultrasonically oscillate for 20 minutes at a vibration frequency of 40 kHz and a power of 120 W to obtain a stable suspension. Nickel foam sheet (such as figure 1 Shown) as the positive electrode, nickel sheet as the negative electrode, put into the above suspension. The distance between the positive and negative plates is 1cm, a voltage of 50V is applied between the plates, and the electrophoretic deposition time is 4 minutes. Put the nickel foam deposited with diamond micropowder into a vacuum oven at 70° C. for 10 minutes to dry. Using a constant temperature water bath, make the concentration of nickel chloride 90g per liter, sodium hypophosphite 30g, ammonium chloride 150g, the temperature of the electroless plating solution whose pH value is adjusted to 8 with ammonia hydrate is kept at 80°C, and the above-mentioned foamed nickel is suspended in ...
Embodiment 2
[0029] Disperse 50 grams (1 mm) of micropowder diamond in 1 liter of ethanol, add 0.8 g of sodium dodecylbenzenesulfonate, and ultrasonically oscillate for 30 minutes at a vibration frequency of 60 kHz and a power of 200 W to obtain a stable suspension. The foamed nickel sheet is used as the positive electrode, and the nickel sheet is used as the negative electrode, which are put into the suspension. The distance between the positive and negative plates is 1cm, a voltage of 10V is applied between the plates, and the electrophoretic deposition time is 1 minute. Put the nickel foam deposited with diamond micropowder into a vacuum oven at 70° C. for 10 minutes to dry. Utilize constant temperature water bath, make the concentration be that every liter contains 80g of nickel chloride, 40g of sodium hypophosphite, 140g of ammonium chloride, the temperature of the electroless plating solution whose pH value is adjusted to 7 with ammonium hydrate is kept at 85 ℃, and above-mentioned n...
Embodiment 3
[0032] Disperse 1 gram (1 mm) of micropowder diamond in 1 liter of ethanol, add 0.5 gram of sodium dodecylbenzenesulfonate, and ultrasonically oscillate for 10 minutes at a vibration frequency of 100 kHz and a power of 60 W to obtain a stable suspension. The foamed nickel sheet is used as the positive electrode, and the nickel sheet is used as the negative electrode, which are put into the suspension. The distance between the positive and negative plates is 1cm, a voltage of 100V is applied between the plates, and the electrophoretic deposition time is 10 minutes. Put the nickel foam deposited with diamond micropowder into a vacuum oven at 70° C. for 10 minutes to dry. Using a constant temperature water bath, make the concentration of nickel chloride 100g per liter, sodium hypophosphite 20g, ammonium chloride 160g, the temperature of the electroless plating solution whose pH value is adjusted to 7.5 with ammonia hydrate is kept at 75°C, and the above-mentioned foamed nickel is...
PUM
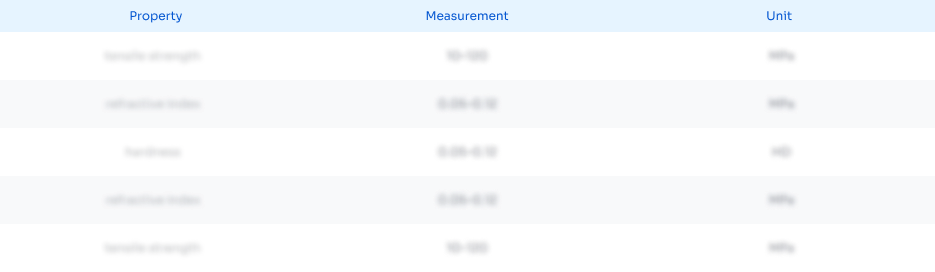
Abstract
Description
Claims
Application Information

- R&D Engineer
- R&D Manager
- IP Professional
- Industry Leading Data Capabilities
- Powerful AI technology
- Patent DNA Extraction
Browse by: Latest US Patents, China's latest patents, Technical Efficacy Thesaurus, Application Domain, Technology Topic, Popular Technical Reports.
© 2024 PatSnap. All rights reserved.Legal|Privacy policy|Modern Slavery Act Transparency Statement|Sitemap|About US| Contact US: help@patsnap.com