Stimulation and vibration pick integrated pressure sensor of electric heating stimulation-piezoresistance vibration pick resonance beam
A technology of pressure sensors and resonant beams, applied in the measurement of force by measuring the frequency change of the stressed vibration element, piezoelectric/electrostrictive/magnetostrictive devices, and the measurement of the property force of piezoelectric resistive materials, etc. , can solve problems such as coupling interference, achieve the effects of simplifying the sensor structure, improving measurement accuracy, and reducing natural frequency drift
- Summary
- Abstract
- Description
- Claims
- Application Information
AI Technical Summary
Problems solved by technology
Method used
Image
Examples
Embodiment Construction
[0019] like figure 2 As shown, the sensitive structure of the electrothermal excitation-piezoresistive pickup resonance beam pressure sensor involving excitation and vibration pickup in the present invention uses silicon as the material, and mainly includes a pressure-sensitive diaphragm 1, a double-ended fixed-supported resonance beam 2, an excitation- The pickup resistor 3 and the phase-locked closed-loop circuit 4; the double-ended fixed support resonant beam 2 is fixed on the upper surface of the pressure-sensitive diaphragm 1, and the measured pressure directly acts on the lower surface of the pressure-sensitive diaphragm 1 and makes the pressure-sensitive diaphragm 1 Deformation occurs, and the deformation of the pressure-sensitive diaphragm 1 causes the internal stress of the double-ended fixed-supported resonant beam 2 to change, thereby changing its natural frequency. Tracking and detecting the natural frequency of the resonant beam 2 can convert the measured pressure...
PUM
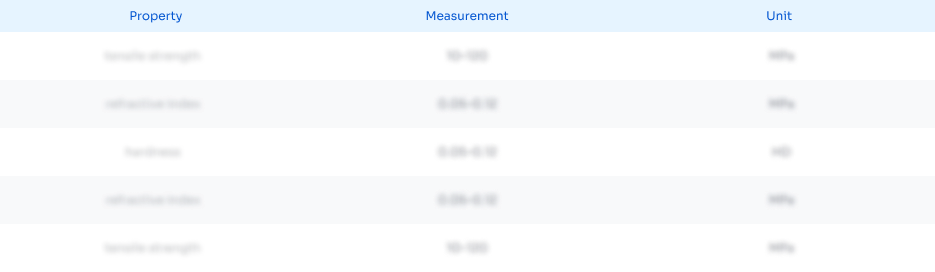
Abstract
Description
Claims
Application Information

- Generate Ideas
- Intellectual Property
- Life Sciences
- Materials
- Tech Scout
- Unparalleled Data Quality
- Higher Quality Content
- 60% Fewer Hallucinations
Browse by: Latest US Patents, China's latest patents, Technical Efficacy Thesaurus, Application Domain, Technology Topic, Popular Technical Reports.
© 2025 PatSnap. All rights reserved.Legal|Privacy policy|Modern Slavery Act Transparency Statement|Sitemap|About US| Contact US: help@patsnap.com