TiC steel-bonded cemented carbide and its manufacturing method
A technology for steel-bonded cemented carbide and cemented carbide rods, which is applied in the field of TiC-based steel-bonded cemented carbide and its preparation, and can solve the problem of large difference in manganese content between surface and core, large difference between surface and core, and resistance to thermal stress. Problems such as poor ability to achieve high grinding efficiency, uniform internal structure, and good ball milling effect
- Summary
- Abstract
- Description
- Claims
- Application Information
AI Technical Summary
Problems solved by technology
Method used
Image
Examples
Embodiment 1
[0009] Example 1: The percentage by weight (i.e. wt%, the following examples are all the same) is 56% TiC, 44% high manganese steel according to the requirements, Ni 4.5%, Mo 2.1%, Mn 14.2%, C 1.1%, Fe balance. Using cemented carbide rods as the grinding body, the ratio of ball to material is 6:1, using alcohol as the medium, adding molding agent and raw materials together for ball milling for 28 hours, then unloading, then spray drying and granulation, then press molding, and finally sintering , to obtain the TiC steel-bonded cemented carbide of the present application, its typical metallographic diagram is shown in figure 1 , the properties are shown in Table 1.
Embodiment 2
[0010] Example 2: The weight percentage (ie wt%, the following examples are all the same) is 54% TiC and 46% high manganese steel according to the requirements, and the high manganese steel contains Ni4.2%, Mo 2.0%, Mn 14.8% , C 1.0%, Fe balance. Using cemented carbide rods as the grinding body, the ratio of ball to material is 6:1, using alcohol as the medium, adding molding agent and raw materials together for ball milling for 28 hours, then unloading, then spray drying and granulation, then press molding, and finally sintering , to obtain the TiC steel-bonded cemented carbide of the present application, its typical metallographic diagram is shown in figure 1 , the properties are shown in Table 1.
Embodiment 3
[0011] Example 3: The percentage by weight (i.e. wt%, the following examples are all the same) is 60% TiC, 40% high manganese steel according to the requirements, and the high manganese steel contains Ni 4.9%, Mo 1.9%, Mn 13.5%, C 1.2%, Fe balance. Using cemented carbide rods as the grinding body, the ratio of ball to material is 6:1, using alcohol as the medium, adding molding agent and raw materials together for ball milling for 28 hours, then unloading, then spray drying and granulation, then press molding, and finally sintering , to obtain the TiC steel-bonded cemented carbide of the present application, its typical metallographic diagram is shown in figure 1 , the properties are shown in Table 1.
[0012] Table 1 Performance comparison between the TiC-based steel-bonded cemented carbide of the present invention and a certain patent application alloy
[0013]
[0014] Depend on figure 1 , figure 2 It can be seen from the comparison that the TiC-based steel-bonded ...
PUM
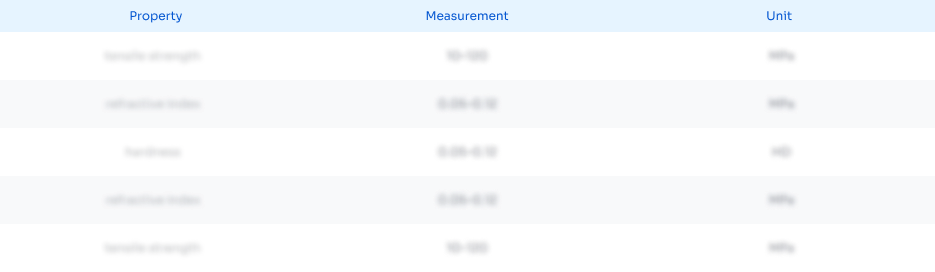
Abstract
Description
Claims
Application Information

- R&D
- Intellectual Property
- Life Sciences
- Materials
- Tech Scout
- Unparalleled Data Quality
- Higher Quality Content
- 60% Fewer Hallucinations
Browse by: Latest US Patents, China's latest patents, Technical Efficacy Thesaurus, Application Domain, Technology Topic, Popular Technical Reports.
© 2025 PatSnap. All rights reserved.Legal|Privacy policy|Modern Slavery Act Transparency Statement|Sitemap|About US| Contact US: help@patsnap.com