Carbon fiber reinforced composite material and preparation technology thereof
A technology for reinforced composite materials and a preparation process, which is applied in the field of carbon fiber reinforced composite materials and their manufacturing processes, can solve the problems affecting the performance of carbon fiber composite materials, restricting the promotion and application of materials, and poor quality of composite materials, and achieves maintaining strength and light weight. , good durability and flexibility
- Summary
- Abstract
- Description
- Claims
- Application Information
AI Technical Summary
Problems solved by technology
Method used
Examples
Embodiment 1
[0023] (1) Pretreatment of carbon fiber:
[0024] Composite pretreatment solution is prepared. The composite pretreatment solution is calculated by weight percentage and consists of the following components: 50% nitric acid, 40% sodium nitrate, and 10% hydrogen peroxide. Pretreatment solution: Soak the mixed fiber carbon fiber braid to be treated in the prepared composite pretreatment solution, and treat it for 40 minutes at a reaction temperature of 60°C, then take it out and wash it fully with sodium hydroxide solution and water. Until the pH value is not acidic, it is dried at 90°C.
[0025] (2) Compression molding
[0026] The molding method is adopted, the mold is divided into upper and lower molds, and the heating jacket is wrapped outside to realize heating. The temperature is controlled by a thermocouple, and the temperature rise rate is adjusted by a transformer. The dimension of the inner cavity of the mold is 1200×800×30mm. Put it into the pre-cleaned molding mold...
Embodiment 2
[0031] (1) Pretreatment of carbon fiber:
[0032] Prepare composite pretreatment solution, composite pretreatment solution is by weight percentage, is made up of following components: 60% nitric acid, 10% acidic potassium dichromate, 15% sodium nitrate, 15% hydrogen peroxide after preparing according to proportion, Add water to prepare a composite pretreatment solution with a concentration of 60%. Soak the multiaxial warp-knitted carbon fiber braid to be treated in the prepared composite pretreatment solution, and treat it for 35 minutes at a reaction temperature of 55°C. , take it out and wash it thoroughly with sodium hydroxide solution and water until the pH value is not acidic, and then dry it at 80°C.
[0033] (2) Compression molding
[0034] The compression molding method is adopted, the mold is divided into upper and lower molds, and the heating jacket is wrapped outside to realize heating. The temperature is controlled by a thermocouple, and the temperature rise rate ...
PUM
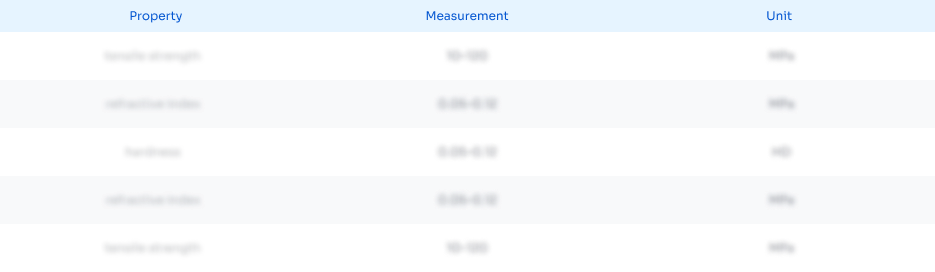
Abstract
Description
Claims
Application Information

- R&D
- Intellectual Property
- Life Sciences
- Materials
- Tech Scout
- Unparalleled Data Quality
- Higher Quality Content
- 60% Fewer Hallucinations
Browse by: Latest US Patents, China's latest patents, Technical Efficacy Thesaurus, Application Domain, Technology Topic, Popular Technical Reports.
© 2025 PatSnap. All rights reserved.Legal|Privacy policy|Modern Slavery Act Transparency Statement|Sitemap|About US| Contact US: help@patsnap.com