Method for pretreating lead base inert anode for electro-deposit copper
An inert anode and pretreatment technology, applied in the direction of electrodes, electrolysis process, electrolysis components, etc., can solve the problems of high power consumption, cost increase, unfavorable energy saving and emission reduction strategy of copper electrowinning, etc., and achieve the reduction of power consumption per ton of copper, operation Convenience, effect of reducing lead content of cathode copper impurities
- Summary
- Abstract
- Description
- Claims
- Application Information
AI Technical Summary
Problems solved by technology
Method used
Image
Examples
Embodiment 1
[0028] The pretreatment liquid composition and pretreatment process parameters of this embodiment are shown in Table 2.
[0029] The Pb-Ca-Sn anode treated by this pretreatment process is used as the anode of electrolytic copper, and after electrolysis in copper electrolytic solution for 10 days, its oxygen evolution overpotential is stable at 545mV.
[0030] The pretreatment liquid composition of table 2 embodiment 1 and pretreatment process parameter
[0031]
Embodiment 2
[0033] The pretreatment solution composition and pretreatment process parameters of this embodiment are shown in Table 3.
[0034] The pretreatment liquid composition of table 3 embodiment 2 and pretreatment process parameter
[0035]
[0036] The Pb-Ca-Sn anode treated by this pretreatment process is used as the anode of electrolytic copper, and after electrolysis in copper electrolytic solution for 10 days, its oxygen evolution overpotential is stable at 530mV.
Embodiment 3
[0038] The pretreatment solution composition and pretreatment process parameters of this embodiment are shown in Table 4.
[0039] The pretreatment liquid composition of table 4 embodiment 3 and pretreatment process parameter
[0040]
[0041] The Pb-Ca-Sn anode treated by this pretreatment process is used as the anode of electrolytic copper, and after electrolysis in copper electrolytic solution for 10 days, its oxygen evolution overpotential is stable at 510mV.
PUM
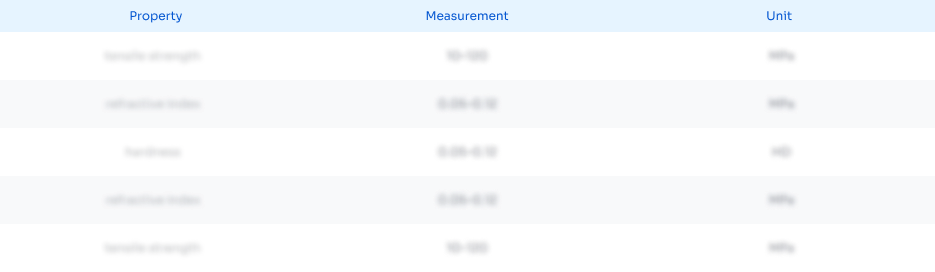
Abstract
Description
Claims
Application Information

- R&D
- Intellectual Property
- Life Sciences
- Materials
- Tech Scout
- Unparalleled Data Quality
- Higher Quality Content
- 60% Fewer Hallucinations
Browse by: Latest US Patents, China's latest patents, Technical Efficacy Thesaurus, Application Domain, Technology Topic, Popular Technical Reports.
© 2025 PatSnap. All rights reserved.Legal|Privacy policy|Modern Slavery Act Transparency Statement|Sitemap|About US| Contact US: help@patsnap.com