Smelting synthetic slag and production method thereof
A production method and technology for synthesizing slag, applied in the direction of improving process efficiency, etc., can solve the problems of serious environmental pollution, large equipment investment, and large material loss, and achieve good effect, good fluidity, and low material loss.
- Summary
- Abstract
- Description
- Claims
- Application Information
AI Technical Summary
Problems solved by technology
Method used
Examples
Embodiment Construction
[0010] The smelting synthetic slag and the production method thereof of the present invention are realized in this way, and are described in detail below. The technical solution provided by the invention is a sintering type synthetic compound that is not easy to break and pulverize, has little dust during use, good fluidity, less material loss, fast melting, good effect, environmental protection, low energy consumption and low production cost. Slag and its production method.
[0011] The smelting synthetic slag of the present invention and its production method are composed of the following components by weight percentage:
[0012] CaO 61%; Al 2 o 3 20%; SiO 2 ≤3%; Fe 2 o 3 ≤1%; MgO≤1%; P≤0.03%; S≤0.01%; CaF 2 ≤2.5%; moisture ≤10%;
[0013] production method:
[0014] Raw materials by weight ratio: CaO 61kg, Al 2 o 3 Grind 20kg into powder, add: water 10kg, SiO 2 3kg, Fe 2 o 3 1kg, MgO 1kg, made into balls, particle size 50mm; fired in a furnace at high temper...
PUM
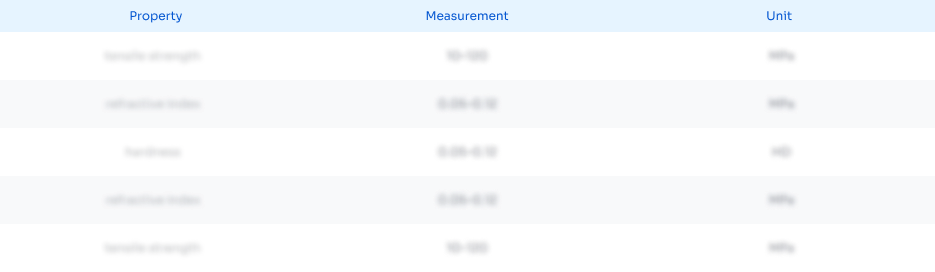
Abstract
Description
Claims
Application Information

- R&D Engineer
- R&D Manager
- IP Professional
- Industry Leading Data Capabilities
- Powerful AI technology
- Patent DNA Extraction
Browse by: Latest US Patents, China's latest patents, Technical Efficacy Thesaurus, Application Domain, Technology Topic, Popular Technical Reports.
© 2024 PatSnap. All rights reserved.Legal|Privacy policy|Modern Slavery Act Transparency Statement|Sitemap|About US| Contact US: help@patsnap.com