Method for manufacturing IMC (Intermetallic Compound) silicon nitride ceramic-based composite brake pad
A technology of silicon nitride ceramics and a manufacturing method, which is applied to friction linings, mechanical equipment and other directions, can solve problems such as friction overheating and wear, and achieve the effects of low average wear rate, simple process and excellent friction coefficient
- Summary
- Abstract
- Description
- Claims
- Application Information
AI Technical Summary
Problems solved by technology
Method used
Examples
Embodiment 1
[0024] Will Fe 3 Al / Si 3 N 4 The composite material was added to a planetary high-energy ball mill with a resin tank as a ball mill for ball milling and mixing. The ball milling time was 4 hours, and the ball mill speed was 380 r / min; the prepared Fe 3Al / Si 3 N 4 The composite material was ground to a fineness of 1200 mesh, and then the Fe 3 Al / Si 3 N 4 82 parts of composite material, 15 parts of graphite powder, Al 2 o 3 3 parts of powder, mixed evenly in a ball mill, and placed in a 60cm×60cm×20cm graphite mold, vacuum hot pressing sintering temperature: 1300°C, heating rate: 5-20°C / min, axial pressure: 5-20 MPa, holding time: 10-60min, after cooling naturally with the furnace; that is, Fe 3 Al / Si 3 N 4 Based on the raw material of composite brake pads, according to the size of the automobile brake pads, use a diamond cutting machine or a wire electric discharge machine to 3 Al / Si 3 N 4 The base composite brake pad raw material is processed and cut into small a...
Embodiment 2
[0026] Preparation of Fe by Mechanical Alloying 3 Al / Si 3 N 4 composite material, and the prepared Fe 3 Al / Si 3 N 4 The composite material was ground to a fineness of 1200 mesh, and then the Fe 3 Al / Si 3 N 4 92 parts of composite material, 5 parts of graphite powder, Al 2 o 3 3 parts of powder are ball milled and mixed evenly, placed in a graphite mold of 60cm×60cm×20cm, vacuum hot-pressed and sintered to 1350°C, the heating rate is 15°C / min, the axial pressure is 5-20 MPa, and the holding time is 10-60min , the product naturally cooled with the furnace is Fe 3 Al / Si 3 N 4 According to the tonnage of medium-sized automobiles, the required brake pads are designed, and the obtained Fe 3 Al / Si 3 N 4 The base composite brake pad raw material is processed into an automobile brake pad of suitable shape, which is the final product, and is used for a medium-sized automobile brake pad of 1.5 tons.
Embodiment 3
[0028] Preparation of Fe by Mechanical Alloying 3 Al / Si 3 N 4 Composite material, the prepared Fe 3 Al / Si 3 N 4 The composite material was ground to a fineness of 1200 mesh, and the Fe 3 Al / Si 3 N 4 87 parts of composite material, 10 parts of graphite powder, Al 2 o 3 Mix 3 parts of the powder by ball milling evenly, place in a graphite mold of 100cm×100cm×30cm, carry out vacuum hot pressing and sintering to 1350°C, heating rate: 12°C / min, axial pressure: 10 MPa, holding time: 40min , the product naturally cooled with the furnace is Fe 3 Al / Si 3 N 4 According to the design requirements of automobile brakes, the raw materials obtained above are processed into a suitable shape, which is the final product, which is used as brake discs and drum pads for small and medium-sized automobiles.
PUM
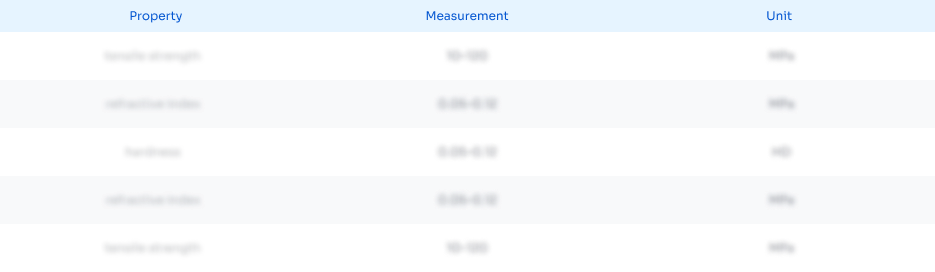
Abstract
Description
Claims
Application Information

- Generate Ideas
- Intellectual Property
- Life Sciences
- Materials
- Tech Scout
- Unparalleled Data Quality
- Higher Quality Content
- 60% Fewer Hallucinations
Browse by: Latest US Patents, China's latest patents, Technical Efficacy Thesaurus, Application Domain, Technology Topic, Popular Technical Reports.
© 2025 PatSnap. All rights reserved.Legal|Privacy policy|Modern Slavery Act Transparency Statement|Sitemap|About US| Contact US: help@patsnap.com