Preparation method of alkyl transferring catalyst
A technology of transalkylation and catalyst, applied in molecular sieve catalysts, chemical instruments and methods, physical/chemical process catalysts, etc., can solve the problems of low transalkylation performance, low benzene/propylene ratio, low reaction temperature, etc. Strong acidity, high activity and good selectivity
- Summary
- Abstract
- Description
- Claims
- Application Information
AI Technical Summary
Problems solved by technology
Method used
Image
Examples
Embodiment 1
[0025] Take by weighing 200g of the former powder of HMCM-49 molecular sieve produced by Jilin University, 100g of imported SB powder, 10g of kale powder, and 10g of methyl cellulose and mix them with 200g of 15% aqueous nitric acid solution. After granulation and extrusion, the extrusion pressure is 150N, the wet strips are placed on the enamel plate, and dried at 120°C for 5.6h; after drying, they are transferred to the roasting pan and roasted in the muffle furnace, and the roasting temperature is programmed. The stepwise temperature was 120°C, 450°C and 540°C, the heating rate was 1°C / min, and the catalyst was calcined at 540°C for 320 minutes to prepare the catalyst.
[0026] Put the catalyst into the tubular reactor, the reactor is Φ25*2*900mm, and carry out the reaction of triisopropylbenzene and benzene, the mass percentage of triisopropylbenzene and benzene is 90:10, and the total liquid space velocity is 1.4-1.6h -1 , the reaction temperature is 170-250°C, and the re...
Embodiment 2
[0030] Take by weighing 180g of the former powder of HMCM-22 molecular sieve produced by Jilin University, 90g of imported SB powder, 16g of ammonium phosphate, 8g of scallop powder, and 7g of citric acid. 190g, mix evenly; roll on the rolling machine for 25min, after granulation and extruding, extruding pressure 150N, place the wet strip on the enamel plate, dry at 110°C for 5.2h; after drying, move to the baking tray In this method, the catalyst was calcined in a muffle furnace, the calcining temperature was programmed to rise, the stepwise temperature was 120°C, 450°C and 540°C, the heating rate was 2°C / min, and the catalyst was calcined at 540°C for 7.3h.
[0031] Using the evaluation method of Example 1, the reaction results are shown in Table 2.
[0032] Table II
[0033]
Embodiment 3
[0035] Weigh 100g of HMCM-49 molecular sieve raw powder produced by Jilin University, 100g of HMCM-22 molecular sieve raw powder, 95g of imported SB powder, 6.3g of turnip powder, and 8.5g of citric acid, add 180g of 10% phosphoric acid aqueous solution and mix evenly. Rolling on the press for 30 minutes, granulating and extruding, the extrusion pressure is 150N, the wet strips are placed on the enamel plate, and dried at 115°C for 5.7 hours; after drying, move to the baking pan and roast in the muffle furnace. The calcination temperature was programmed to raise the temperature, the subsection temperature was 120°C, 450°C and 540°C, the heating rate was 2°C / min, and the catalyst was calcined at 540°C for 10 hours to prepare the catalyst.
[0036] Using the evaluation method of Example 1, the reaction results are shown in Table 3.
[0037] Table three
[0038]
PUM
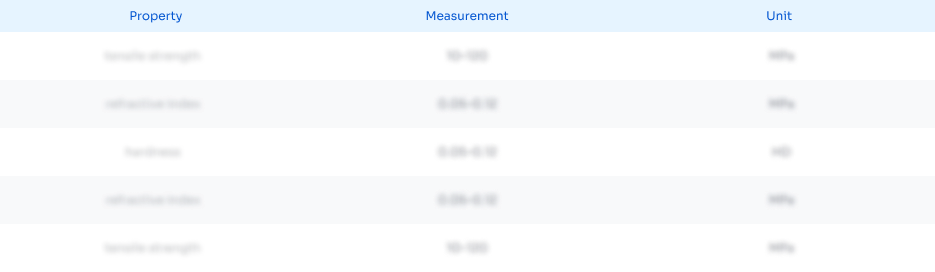
Abstract
Description
Claims
Application Information

- R&D
- Intellectual Property
- Life Sciences
- Materials
- Tech Scout
- Unparalleled Data Quality
- Higher Quality Content
- 60% Fewer Hallucinations
Browse by: Latest US Patents, China's latest patents, Technical Efficacy Thesaurus, Application Domain, Technology Topic, Popular Technical Reports.
© 2025 PatSnap. All rights reserved.Legal|Privacy policy|Modern Slavery Act Transparency Statement|Sitemap|About US| Contact US: help@patsnap.com