Method for preparing paromomycin crude product by membrane separation technology
A paromomycin and membrane separation technology, which is applied in the preparation of sugar derivatives, chemical instruments and methods, sugar derivatives, etc., can solve the problems of loss of ion exchange resin, difficult filtration of fermentation liquid, unshaped filter cake, etc. The effect of reducing emissions, simple process and short working time
- Summary
- Abstract
- Description
- Claims
- Application Information
AI Technical Summary
Problems solved by technology
Method used
Examples
Embodiment 1
[0020] Using 260L of fermented broth with a ribomycin concentration of 5.5g / L as raw material, a ceramic microfiltration membrane with a molecular weight cut-off of 50,000 is used. The flux is 35L / h·㎡, the operating pressure is 2.5bar, and the operating temperature is 35°C. Under operating conditions, bacteria and residues in the fermentation broth are removed. The permeate adopts a composite ultrafiltration membrane with a molecular weight cut-off of 5000. Under the operating conditions of a membrane flux of 30 L / h m2, an operating pressure of 5.0 bar, and an operating temperature of 30°C, impurities are removed through the ultrafiltration membrane to remove proteins, Polysaccharides and color-forming substances, etc. The ultrafiltration permeate is treated by nanofiltration with a composite membrane with a molecular weight cut-off of 300. Under the operating conditions of a nanofiltration membrane flux of 30 L / h m2, an operating pressure of 10.0 bar, and an operating tempera...
Embodiment 2
[0022] Using 350L of fermented broth with a ribomycin concentration of 5.0g / L as raw material, ceramic microfiltration membrane with a molecular weight cut-off of 50,000 is used. The flux is 40L / h·㎡, the operating pressure is 3.0bar, and the operating temperature is 30°C. Under operating conditions, bacteria and residues in the fermentation broth are removed. The permeate adopts a composite ultrafiltration membrane with a molecular weight cut-off of 5000. Under the operating conditions of a membrane flux of 30 L / h m2, an operating pressure of 5.0 bar, and an operating temperature of 30°C, impurities are removed through the ultrafiltration membrane to remove proteins, Polysaccharides and color-forming substances, etc. The ultrafiltration permeate is treated by nanofiltration with a composite membrane with a molecular weight cut-off of 300. Under the operating conditions of the nanofiltration membrane flux of 30 L / h·㎡, the operating pressure of 8.0 bar, and the operating tempera...
Embodiment 3
[0024] Using 35L of powder mother liquor with ribomycin concentration of 98.0g / L as raw material, diluted with purified water to 350L, ceramic microfiltration membrane with a molecular weight cut-off of 50,000 is used, the flux is 40L h·㎡, and the operating pressure is 3.0bar. The impurities in the mother liquor are removed under the operating condition of an operating temperature of 30°C. The permeate adopts a composite ultrafiltration membrane with a molecular weight cut-off of 5000. Under the operating conditions of a membrane flux of 30 L / h·㎡, an operating pressure of 5.0 bar, and an operating temperature of 30°C, impurities are removed through the ultrafiltration membrane to remove color-forming substances. Wait. The ultrafiltration permeate is treated by nanofiltration with a composite membrane with a molecular weight cut-off of 300. Under the operating conditions of the nanofiltration membrane flux of 30 L / h·㎡, the operating pressure of 10.0 bar, and the operating tempe...
PUM
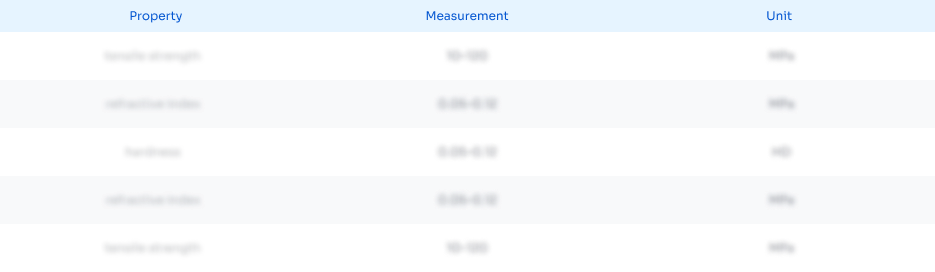
Abstract
Description
Claims
Application Information

- Generate Ideas
- Intellectual Property
- Life Sciences
- Materials
- Tech Scout
- Unparalleled Data Quality
- Higher Quality Content
- 60% Fewer Hallucinations
Browse by: Latest US Patents, China's latest patents, Technical Efficacy Thesaurus, Application Domain, Technology Topic, Popular Technical Reports.
© 2025 PatSnap. All rights reserved.Legal|Privacy policy|Modern Slavery Act Transparency Statement|Sitemap|About US| Contact US: help@patsnap.com