Method for gathering nickel and iron from laterite-nickel ores
A laterite nickel ore enrichment technology, which is applied in the field of nickel laterite ore and low-grade laterite nickel ore to enrich nickel and iron, can solve the problems of retention, large difference in energy consumption cost, and unstable process technology, etc.
- Summary
- Abstract
- Description
- Claims
- Application Information
AI Technical Summary
Problems solved by technology
Method used
Image
Examples
Embodiment 1
[0047] The lateritic nickel ore from the Philippines was used for verification. After the raw ore sample was dried, it was crushed by a closed-circuit crushing process consisting of a jaw crusher, a roller crusher and a -2.5mm sieve. The crushed product was homogenized, fractionated and sampled. The results of multi-component chemical analysis of raw ore are shown in Table 1.
[0048] Table 1 raw ore multi-component chemical analysis results (%)
[0049]
[0050] Nickel extraction test and results
[0051] Test method: Crush laterite nickel ore and anthracite coal powder to -2.0mm, and mix evenly according to the ratio of ore and coal powder 100:20. Spread a layer of 5mm coal powder on the bottom of the rotary hearth furnace, and then spread the mixed mineral powder and coal powder on it for reduction. The thickness of the material layer is 40mm, and the mixed material surface is covered with a 4mm thick protective coal layer. The reduction temperature is 1275°C, and the...
Embodiment 2
[0057] For the above-mentioned laterite nickel ore sample, the laterite nickel ore and anthracite coal powder were crushed to -3.0mm, and mixed evenly according to the ratio of ore and coal powder 100:20. Spread a layer of 5mm coal powder on the bottom of the rotary hearth furnace, and then spread the mixed mineral powder and coal powder on it for reduction. The thickness of the material layer is 40mm, and the mixed material surface is covered with a 4mm thick protective coal layer. The reduction temperature is 1300°C, and the reduction time is 1.0 hour. After the reduction product is cooled, use a magnetic separator to remove excess protective coal in the protective coal seam, and recycle it for reuse. The magnetic separator concentrate is finely ground and then magnetically separated to obtain a mixed product of nickel metal and iron metal.
[0058] Test results: The test results are shown in Table 3.
[0059] Table 3 test results, %
[0060] serial number samp...
Embodiment 3
[0063] For the above-mentioned laterite nickel ore sample, the laterite nickel ore and anthracite coal powder were crushed to -2.5mm, and mixed evenly according to the ratio of ore and coal powder 100:25. No pulverized coal is spread on the bottom of the rotary hearth furnace, and then the mixed pulverized ore and pulverized coal are directly placed in the reduction box for reduction. The thickness of the material layer is 30mm, and the surface of the mixed material is covered with a 4mm thick protective coal layer. The reduction temperature is 1275°C, and the reduction time is 50 minutes. After the reduction product is cooled, use a magnetic separator to remove excess protective coal in the protective coal seam, and recycle it for reuse. The concentrate of the magnetic separator is finely ground and then subjected to two-stage magnetic separation to obtain a mixed product of nickel metal and iron metal.
[0064] Test results: The test results are shown in Table 4.
[0065] ...
PUM
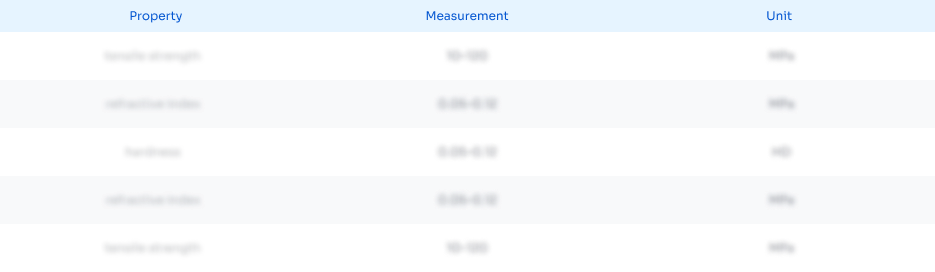
Abstract
Description
Claims
Application Information

- R&D Engineer
- R&D Manager
- IP Professional
- Industry Leading Data Capabilities
- Powerful AI technology
- Patent DNA Extraction
Browse by: Latest US Patents, China's latest patents, Technical Efficacy Thesaurus, Application Domain, Technology Topic, Popular Technical Reports.
© 2024 PatSnap. All rights reserved.Legal|Privacy policy|Modern Slavery Act Transparency Statement|Sitemap|About US| Contact US: help@patsnap.com