Technology of enhanced-dispersion partial selective and bulk flotation of lead and zinc sulfide ores under low and high alkalinity
A technology of mixing flotation and sulfide ore, applied in flotation, solid separation and other directions, can solve the problems of reducing the recovery rate of precious metals, large consumption of chemicals, reducing the recovery rate of lead, etc. frequency, reducing transportation and smelting costs, and improving silver recovery
- Summary
- Abstract
- Description
- Claims
- Application Information
AI Technical Summary
Problems solved by technology
Method used
Image
Examples
Embodiment 1
[0012] A lead-zinc mine in Yunnan contains 1.60% lead, 4.70% zinc, 15% sulfur, and 110g / t silver. The technical indicators obtained by using the conventional high-alkali process are 45.4% lead concentrate grade and 55.3% recovery rate. The silver grade is 2113g / t, and the silver recovery rate is 50.7%; the zinc concentrate grade is 41.5%, and the recovery rate is 88.7%; the sulfur concentrate grade is 33%, and the recovery rate is 61.1%. Adopting the technological process of the present invention, the raw ore is ground to -0.074mm, which accounts for 67%. During the grinding process, 800g / t sodium hexametaphosphate is added as a dispersant and a grinding aid to improve the dispersibility of the pulp and the grinding effect. Add 3000g / t of lime to adjust the pH value to 9.0, use zinc sulfate and sodium sulfite as sphalerite inhibitors, the dosage is 400g / t and 300g / t respectively, the selectivity of galena is better, and that of pyrite and The butyl ammonium black drug and ethy...
Embodiment 2
[0014]A lead-zinc mine in Guangxi contains 2.10% lead, 5.60% zinc, 18% sulfur, and 90g / t silver. The technical indicators obtained by using the conventional high-alkali process are 47.0% lead concentrate grade and 82.1% recovery rate. The silver grade is 1910g / t, and the silver recovery rate is 60.0%; the zinc concentrate grade is 44.3%, and the recovery rate is 88.0%; the sulfur concentrate grade is 35%, and the recovery rate is 63.3%. Adopting the technological process of the present invention, the raw ore is ground to -0.074mm and accounts for 70%, and 1000g / t sodium hexametaphosphate is added as a dispersant and a grinding aid during the grinding process to improve the dispersibility of the pulp and the grinding effect, Add 4000g / t of lime to adjust the pH value to 9.5, use zinc sulfate and sodium sulfite as sphalerite inhibitors, the dosage is 500g / t and 400g / t respectively, the selectivity of galena is better, and that of pyrite and The butyl ammonium black drug and ethy...
Embodiment 3
[0017] A lead-zinc mine in Yunnan contains 1.60% lead, 4.70% zinc, 15% sulfur, and 110g / t silver. The technical indicators obtained by using the conventional high-alkali process are 45.4% lead concentrate grade and 55.3% recovery rate. The silver grade is 2113g / t, and the silver recovery rate is 50.7%; the zinc concentrate grade is 41.5%, and the recovery rate is 88.7%; the sulfur concentrate grade is 33%, and the recovery rate is 61.1%. Adopting the technological process of the present invention, the raw ore is ground to -0.074mm, which accounts for 69%. During the grinding process, 900g / t sodium hexametaphosphate is added as a dispersant and a grinding aid to improve the dispersibility of the pulp and the grinding effect. Add 3500g / t of lime to adjust the pH value to 9.3, use zinc sulfate and sodium sulfite as sphalerite inhibitors, the dosage is 450g / t and 350g / t respectively, the selectivity of galena is better, and that of pyrite and The butyl ammonium black drug and ethy...
PUM
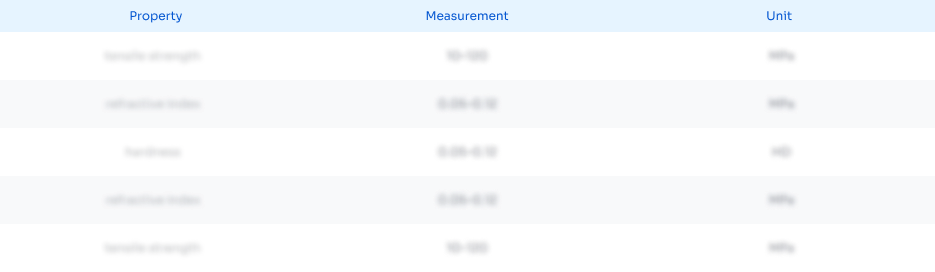
Abstract
Description
Claims
Application Information

- R&D
- Intellectual Property
- Life Sciences
- Materials
- Tech Scout
- Unparalleled Data Quality
- Higher Quality Content
- 60% Fewer Hallucinations
Browse by: Latest US Patents, China's latest patents, Technical Efficacy Thesaurus, Application Domain, Technology Topic, Popular Technical Reports.
© 2025 PatSnap. All rights reserved.Legal|Privacy policy|Modern Slavery Act Transparency Statement|Sitemap|About US| Contact US: help@patsnap.com