Method for melting titanium alloy containing high-melting point alloy element
An alloying element, high melting point technology, applied in the field of titanium alloy preparation, can solve the problems of non-frit inclusion, titanium alloy non-frit, composition deviation, etc., and achieve the effect of reducing current and voltage values, ensuring uniformity, and reducing costs
- Summary
- Abstract
- Description
- Claims
- Application Information
AI Technical Summary
Problems solved by technology
Method used
Image
Examples
Embodiment 1
[0026] Embodiment 1. Preparation of a Ti13Nb13Zr alloy ingot with a diameter of 360 mm
[0027] 1. Ingredients and electrode block pressing
[0028] Sponge titanium, sponge zirconium and pure niobium plate are used as raw materials. According to the nominal composition of the alloy, the addition of elements in the alloy is designed. The sponge titanium and sponge zirconium are weighed and mixed, and the mixture is mixed by an automatic mixing system. The pure Nb plate element The added amount is calculated as 13.2% by weight.
[0029] 2. Electrode preparation
[0030] See attached figure 1 , 2 , the mixture of sponge titanium and sponge zirconium is divided into four equal parts, respectively pressed into four electrode blocks with the same cross-sectional area and equal length, the cross-section of the electrode block is square; then the four electrode blocks are assembled and welded into A consumable electrode, the consumable electrode is composed of a pure Nb plate sand...
Embodiment 2
[0041] Embodiment two, prepare the Ti35Nb4Sn alloy ingot of diameter 280mm specification
[0042] 1. Ingredients and electrode block pressing
[0043] Sponge titanium, titanium tin and pure niobium plate are used as raw materials, the sponge titanium and titanium tin are calculated according to the nominal composition of the alloy, the raw materials are weighed and mixed, and the material is mixed through an automatic mixing system. The addition of pure Nb plate elements is based on weight percentage 35.3% calculated.
[0044] 2. Electrode preparation
[0045] See attached figure 1 , 2 , the mixture of sponge titanium and titanium tin is divided into four equal parts, respectively pressed into four electrode blocks with the same cross-sectional area and equal length, and the cross-section of the electrode block is square; then the four electrode blocks are assembled and welded into A consumable electrode, the consumable electrode is composed of a pure Nb plate sandwiched bet...
example 3
[0056] Example three, preparation of Ti12Mo6Zr2Fe alloy ingot with a diameter of 280 mm
[0057] 1. Ingredients and electrode block pressing
[0058] Using sponge titanium, sponge zirconium, iron nails, and pure Mo plates as raw materials, the sponge titanium, sponge zirconium, and iron nails are calculated according to the nominal composition of the alloy, weighed and mixed, mixed by an automatic mixing system, and pressed into an electrode block. The pure Mo board is calculated at 12.1% by weight.
[0059] 2. Electrode preparation
[0060] See attached figure 1 , 2 , divide the mixture of sponge titanium, sponge zirconium and iron nails into four equal parts, respectively press into four electrode blocks with the same cross-sectional area and equal length, and the cross-section of the electrode blocks is square; then the four electrode blocks Assembled and welded into a consumable electrode, the consumable electrode is composed of a pure Mo plate sandwiched between any t...
PUM
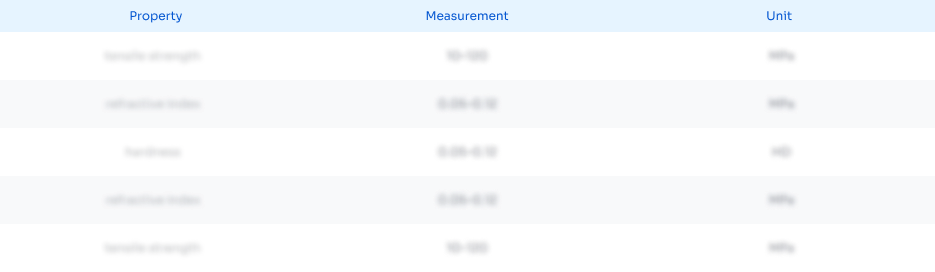
Abstract
Description
Claims
Application Information

- R&D
- Intellectual Property
- Life Sciences
- Materials
- Tech Scout
- Unparalleled Data Quality
- Higher Quality Content
- 60% Fewer Hallucinations
Browse by: Latest US Patents, China's latest patents, Technical Efficacy Thesaurus, Application Domain, Technology Topic, Popular Technical Reports.
© 2025 PatSnap. All rights reserved.Legal|Privacy policy|Modern Slavery Act Transparency Statement|Sitemap|About US| Contact US: help@patsnap.com