High-temperature-resistant electric wire and preparation process thereof
A high-temperature-resistant wire technology, which is applied in the field of high-temperature-resistant wires and its preparation technology, can solve the problems that the long-term working temperature can only reach 200°C and cannot meet the requirements of higher temperature working environments, and achieve improved anti-interference performance and light weight , the effect of small outer diameter
- Summary
- Abstract
- Description
- Claims
- Application Information
AI Technical Summary
Problems solved by technology
Method used
Image
Examples
Embodiment Construction
[0020] Control attached figure 1 , the structure of which is a regular stranded nickel-plated round copper wire conductor 1. The periphery of the conductor 1 is an inner insulating layer 2 wrapped with polyimide composite tape (PTFE / PI / PTFE). The outer periphery of the inner insulating layer is made of a braiding machine Braided high temperature resistant alkali-free glass fiber outer insulation layer 3.
[0021] Control attached figure 2 , the structure of which is a regular stranded nickel-plated round copper wire conductor 1. The periphery of the conductor 1 is an inner insulating layer 2 wrapped with polyimide composite tape (PTFE / PI / PTFE). The outer periphery of the inner insulating layer is made of a braiding machine Braided high temperature resistant alkali-free glass fiber outer insulation layer 3.
[0022] The periphery of the high-temperature-resistant alkali-free glass fiber outer insulation layer 3 woven by a braiding machine is a nickel-plated round copper wire...
PUM
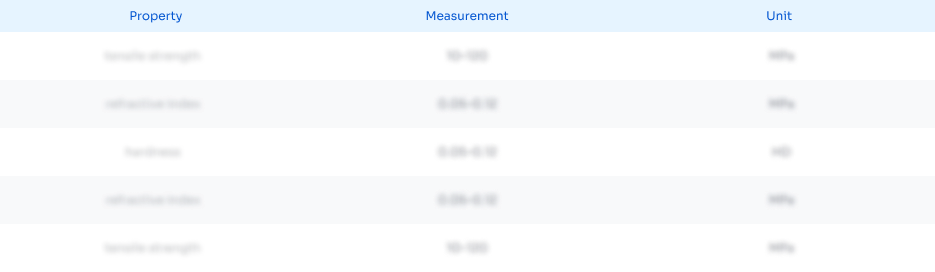
Abstract
Description
Claims
Application Information

- R&D
- Intellectual Property
- Life Sciences
- Materials
- Tech Scout
- Unparalleled Data Quality
- Higher Quality Content
- 60% Fewer Hallucinations
Browse by: Latest US Patents, China's latest patents, Technical Efficacy Thesaurus, Application Domain, Technology Topic, Popular Technical Reports.
© 2025 PatSnap. All rights reserved.Legal|Privacy policy|Modern Slavery Act Transparency Statement|Sitemap|About US| Contact US: help@patsnap.com