Copper alloy material for textile plant water treatment and preparation method thereof
A copper alloy and water treatment technology, applied in anodizing and other directions, can solve the problems of holes or pinholes, increase in dosage, scaling and corrosion of heat exchange equipment, and achieve beneficial corrosion resistance, cost-effective treatment, and oxidation process. simple effect
- Summary
- Abstract
- Description
- Claims
- Application Information
AI Technical Summary
Problems solved by technology
Method used
Examples
Embodiment 1
[0016] Copper alloy for water treatment in textile mills, the mass percentage of each component is: aluminum 5%, magnesium 4%, titanium 6%, nickel 5%, iron 5%, manganese 0.01%, La0.01%, and the balance is copper and unavoidable impurities.
[0017] Carry out anodic oxidation to above-mentioned copper alloy: Oxidizing solution one is: Na 3 PO 4 8g / L, K 2 HPO 4 1g / L, 1g / L(NH4) 3 RhCl 6 ;The current density is 1A / dm 2 , time 100min, temperature 75°C.
[0018] Or the oxidizing solution is Na 3 PO 4 12g / L, K 2 HPO 4 5g / L, 5g / L(NH4) 3 RhCl 6 ;The current density is 3A / dm 2 , time 80min, temperature 50°C.
[0019] The preparation method of the above-mentioned copper alloy comprises the following steps: ① adding the raw material metal components into the graphite crucible that has been burned to deep red according to the required ratio; ② stirring and mixing the raw materials to form a uniform melt after the raw materials are melted, And add 0.03% manganese chloride...
Embodiment 2
[0021] The copper alloy used for water treatment in textile mills prepared by the present invention has the following mass percentages of its components: 10% aluminum, 8% magnesium, 15% titanium, 10% nickel, 10% iron, 0.1% manganese, 0.15% praseodymium, and The amount is copper and unavoidable impurities.
[0022] The micro-arc oxidation process is: oxidizing solution component one: Na 2 SiO 3 12g / L, Na 2 B 4 o 7 12g / L, K 2 HPO 4 5g / L, (NH4) 3 RhCl 6 5g / L; Niacin 5g / L, current density 20A / dm 2 , time 5min, temperature 40°C.
[0023] Or oxidizing solution component two: Na 2 SiO 3 8g / L, Na 2 B 4 o 7 8g / L, K 2 HPO 4 1g / L, 1g / L(NH4) 3 RhCl 6 ; Niacin 1g / L, current density 15A / dm 2 , time 9min, temperature 60°C.
[0024] The preparation method of the above-mentioned copper alloy comprises the following steps: ① adding the raw material metal components into the graphite crucible that has been burned to deep red according to the required ratio; ② stirring ...
PUM
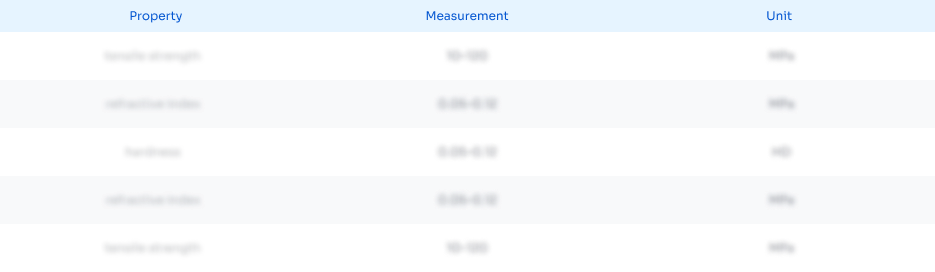
Abstract
Description
Claims
Application Information

- R&D Engineer
- R&D Manager
- IP Professional
- Industry Leading Data Capabilities
- Powerful AI technology
- Patent DNA Extraction
Browse by: Latest US Patents, China's latest patents, Technical Efficacy Thesaurus, Application Domain, Technology Topic, Popular Technical Reports.
© 2024 PatSnap. All rights reserved.Legal|Privacy policy|Modern Slavery Act Transparency Statement|Sitemap|About US| Contact US: help@patsnap.com