Method for producing zinc sulfate heptahydrate, crude tin and crude lead by using tin smelting dust
A technology of zinc sulfate heptahydrate and soot, applied in the field of non-ferrous metal smelting wet-fire combined process, can solve the problems of low reverberatory furnace smelting temperature, low tin remelting direct yield, uneven furnace temperature, etc. The effect of easy industrialization implementation, strong principle adaptability and reasonable process structure
- Summary
- Abstract
- Description
- Claims
- Application Information
AI Technical Summary
Problems solved by technology
Method used
Image
Examples
Embodiment 1
[0041] Example 1: Raw material electric furnace tin fume main chemical composition mass percentage (mass%): Sn 19.78, Pb 12.30, Zn 26.32, Cu 0.35, As 1.69, Sb 0.62, S 1.25, FeO 1.41, CaO 1.12, SiO2 1.40, Al2O3 1.68 .
[0042] (1) Dehydrate the raw materials to less than 5% by mass, and screen out iron nuggets, slag and other impurities of ≥8-10mm entrained by the machine.
[0043] (2) Under normal temperature and stirring conditions, use the No. 1 12m3 stirring tank for the 1st stage leaching of electric furnace tin fume; first pump into the No. 1 storage tank to process about 10m3 of the second leaching solution of the previous batch of materials, start the mixer, and put in each tank Add 1.25t of industrial sulfuric acid to 3.5t of electric furnace tin fume raw material, add leaching solution twice to a total volume of 12 m3, solid: liquid = 1:3.4 (t:m3), stir and leaching for 2.5h, and the final pH value is 2.5. The leaching slurry is transported by a 65-Z×B-40 self-primin...
Embodiment 2
[0049] Example 2: Raw material reverberatory furnace tin smoke main chemical composition mass percentage (mass %): Sn 28.28, Pb 10.59, Zn 12.45, Cu 0.18, As 0.96, Sb 0.01, S 1.96, slagging elements 16-22.
[0050] (1) Dry the raw materials until the water content is less than 5% by mass, and screen out the massive debris ≥ 8mm entrained by the machine.
[0051] (2) Under normal temperature and stirring conditions, use No. 1 stirring tank as the first-stage leaching of tin fume in the reverberatory furnace. Use the leaching solution twice to adjust the slurry, put 4.8t of raw material of reverberatory furnace tin fume into each tank (time), add 0.86t of industrial sulfuric acid, solid: liquid = 1:2.5 (t:m3), stir and leaching for 2 hours and press filter to obtain a concentration of 29 oBe, crude zinc sulfate solution with pH 2.0 and 1 leaching residue. Quality composition of zinc solution (mass g / L): Zn 82~85, Sn 2.12~2.94, Pb 0.12~0.16, Cu 1.04~1.26, Fe 0.11~0.13, Sb 0.02~0....
Embodiment 3
[0057] Example 3: Raw material secondary (electric furnace) tin fume main chemical composition mass percentage (mass%): Sn 25.24, Pb 2.42, Zn 34.74, Cu 0.30, As 2.41, Sb 0.18, S 0.75, FeO 1.08, CaO 0.34, SiO2 2.51, Al2O3 1.48.
[0058] (1) Dehydrate the raw material to less than 5% by mass, and screen out the massive entrainment ≥ 8mm.
[0059] (2) Under the condition of normal temperature and stirring, the secondary tin fume 1 stage leaching is carried out in the No. 1 stirring tank. Use 2 leaching liquids to adjust slurry, put in 2.8t / tank of secondary tin fume raw material, add industrial sulfuric acid 1.05t / tank, solid:liquid=1:4.3 (t:m3), stir and leaching for 2.5h and press filter to obtain a concentration of 32 oBe, crude zinc sulfate solution with pH 2.5 and 1 leaching residue. The mass composition of the zinc solution (mass g / L): Zn 86-90, Sn 0.96-1.68, Pb 0.11-0.13, Cu 1.32-1.64, Fe 0.13-0.15, Sb 0.08-0.12, sent to the copper removal process for treatment. The 1st...
PUM
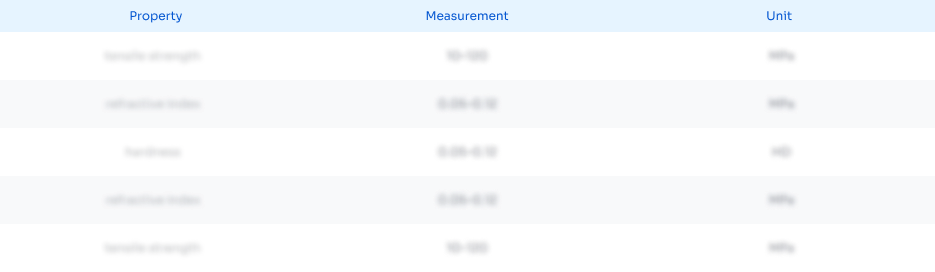
Abstract
Description
Claims
Application Information

- R&D
- Intellectual Property
- Life Sciences
- Materials
- Tech Scout
- Unparalleled Data Quality
- Higher Quality Content
- 60% Fewer Hallucinations
Browse by: Latest US Patents, China's latest patents, Technical Efficacy Thesaurus, Application Domain, Technology Topic, Popular Technical Reports.
© 2025 PatSnap. All rights reserved.Legal|Privacy policy|Modern Slavery Act Transparency Statement|Sitemap|About US| Contact US: help@patsnap.com