A concrete delivery pipe and its manufacturing method
A technology for concrete conveying pipes and elbows, used in siphons, pipe elements, flange connections, etc.
- Summary
- Abstract
- Description
- Claims
- Application Information
AI Technical Summary
Problems solved by technology
Method used
Image
Examples
Embodiment Construction
[0034] Such as Figure 1-Figure 13 As shown, the concrete delivery pipe includes an elbow 100 and a straight pipe 200, and the straight pipe 200 is connected to the elbow 100; Set in the curved outer pipe 1, there is a filling layer 8 between the curved wear-resistant pipe 2 and the curved outer pipe 1, the curved pipe flange 4 is connected to the curved outer pipe 1, and the curved pipe flange 4 has a curved pipe inner sleeve 3, Bonding between the elbow inner sleeve 3 and the elbow flange 4 . The straight pipe 200 includes a straight wear-resistant pipe 12, a straight outer pipe 11 and a straight pipe flange 13, the straight wear-resistant pipe 12 is placed in the straight outer pipe 11, and the straight wear-resistant pipe 12 is bonded to the straight outer pipe 11; The pipe flange 13 is connected with the straight outer pipe 11, and the straight pipe flange 13 has a straight pipe inner sleeve 14, and the straight pipe inner sleeve 14 is bonded to the straight pipe flange ...
PUM
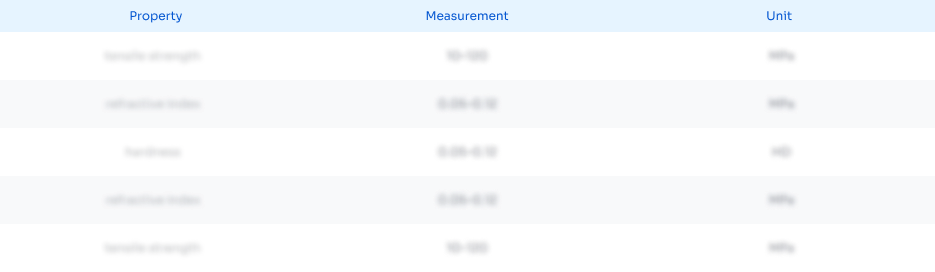
Abstract
Description
Claims
Application Information

- R&D Engineer
- R&D Manager
- IP Professional
- Industry Leading Data Capabilities
- Powerful AI technology
- Patent DNA Extraction
Browse by: Latest US Patents, China's latest patents, Technical Efficacy Thesaurus, Application Domain, Technology Topic, Popular Technical Reports.
© 2024 PatSnap. All rights reserved.Legal|Privacy policy|Modern Slavery Act Transparency Statement|Sitemap|About US| Contact US: help@patsnap.com