Method for making V-shaped groove texture surface on surface of monocrystalline silicon solar cell
A technology for solar cells and monocrystalline silicon, applied in chemical instruments and methods, circuits, crystal growth, etc., can solve the problems of uneven inner surface, easy contamination of silicon wafers, low processing efficiency, etc., and achieve quality improvement and texturing efficiency. High, yield-enhancing effect
- Summary
- Abstract
- Description
- Claims
- Application Information
AI Technical Summary
Problems solved by technology
Method used
Image
Examples
preparation example Construction
[0060] Concrete preparation process is as follows:
[0061] A. First evacuate the vacuum chamber to make the vacuum degree better than 5*10 -4 ;
[0062] B. Then use high-purity argon (Ar, 99.9999Vol%) to make the pressure of the vacuum chamber reach 0.3Pa;
[0063] C. Sputter and clean the single crystal Si wafer (sputter power 100W) for 15 minutes;
[0064] D. Pre-sputter the composite target for 30 minutes;
[0065] E. After the pre-sputtering, first sputter-deposit Cu-Zr alloy film on the single crystal Si (100) substrate;
[0066] F. Deposit a layer of pure Cu film on the surface of the prepared Cu-Zr alloy film to form a composite structure of Cu / Cu-Zr / monocrystalline silicon Si (100);
[0067] Sputtering power: 50-200W, the sputtering power can also be adjusted according to the required growth rate. By adjusting the process parameters, Cu-Zr (0.5-35at.%Zr) alloy film can be prepared, and the film thickness is between 10nm and 5 microns between.
[0068] 2. Anneali...
Embodiment 1
[0077] 1. First, a 450nm thick Cu-15.6at%Zr alloy film and a 100nm thick pure Cu film were sequentially deposited on single crystal Si (100) by magnetron sputtering to form a Cu / Cu-Zr / Si(100) composite Membrane-based system;
[0078] 2. Then, for the Cu / Cu-Zr / Si(100) composite film base system, at 3×10 -4 Vacuum degree, temperature 520°C, annealing for 1 hour, and cooling with the furnace, the structure of copper-silicon compound formed on the surface of Si is obtained; as figure 2 shown;
[0079] 3. Finally, put the annealed Cu / Cu-Zr / Si(100) composite film-based system into a mixed corrosion solution composed of 85vol% acetone, 5vol% hydrofluoric acid and 10vol% dilute hydrochloric acid, and perform ultrasonic Shake for 30 minutes, take it out after shaking, wash with absolute ethanol and deionized water, and dry with a hair dryer to obtain a V-shaped groove suede structure; Figure 4 shown.
PUM
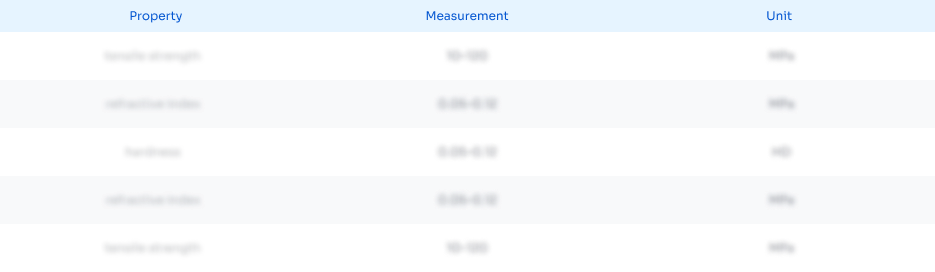
Abstract
Description
Claims
Application Information

- Generate Ideas
- Intellectual Property
- Life Sciences
- Materials
- Tech Scout
- Unparalleled Data Quality
- Higher Quality Content
- 60% Fewer Hallucinations
Browse by: Latest US Patents, China's latest patents, Technical Efficacy Thesaurus, Application Domain, Technology Topic, Popular Technical Reports.
© 2025 PatSnap. All rights reserved.Legal|Privacy policy|Modern Slavery Act Transparency Statement|Sitemap|About US| Contact US: help@patsnap.com