A continuous casting tundish casting residual steel processing device and its method
The technology of continuous casting tundish and treatment device is applied in the field of equipment for the treatment of residual molten steel in steelmaking and continuous casting tundish, which can solve the problems of inability to adapt to production requirements, the influence of surrounding environment, and the large loss of metal iron, so as to reduce the investment in dust removal. and operating costs, saving cutting and processing sites, and reducing the effect of metal iron loss
- Summary
- Abstract
- Description
- Claims
- Application Information
AI Technical Summary
Problems solved by technology
Method used
Image
Examples
Embodiment Construction
[0015] Referring to the accompanying drawings, through the description of the embodiments, the specific embodiments of the present invention include the shape, structure, mutual position and connection relationship of each part, the function and working principle of each part, and the manufacturing process of the various components involved. And the method of operation and use, etc., are described in further detail to help those skilled in the art have a more complete, accurate and in-depth understanding of the inventive concepts and technical solutions of the present invention.
[0016] see Figure 4 It can be seen from the schematic diagram of steel processing that the molten steel in the ladle 5 is poured into the tundish 6, and the bottom of the tundish 6 is provided with an opening and connected to the continuous casting machine 7, which is pulled out to produce the product billet 2. After the tundish 6 is poured into the 2-3 furnaces of molten steel in the ladle 5, in or...
PUM
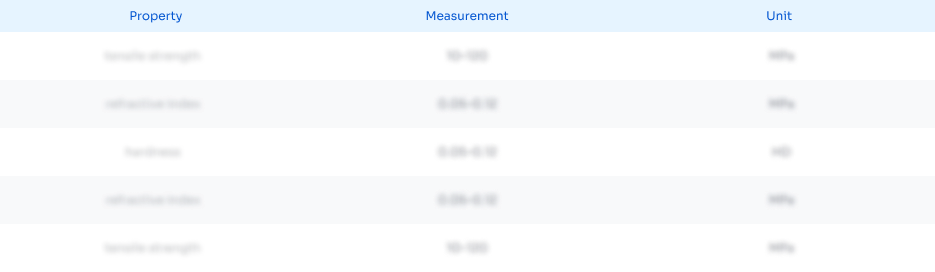
Abstract
Description
Claims
Application Information

- R&D
- Intellectual Property
- Life Sciences
- Materials
- Tech Scout
- Unparalleled Data Quality
- Higher Quality Content
- 60% Fewer Hallucinations
Browse by: Latest US Patents, China's latest patents, Technical Efficacy Thesaurus, Application Domain, Technology Topic, Popular Technical Reports.
© 2025 PatSnap. All rights reserved.Legal|Privacy policy|Modern Slavery Act Transparency Statement|Sitemap|About US| Contact US: help@patsnap.com