Preparation method of ceramsite filter material for water treatment
A ceramsite filter material and water treatment technology, applied in ceramic products, separation methods, chemical instruments and methods, etc., can solve the problem of consuming natural resources bentonite and starch, increasing water head loss in the water treatment process, and poor organic macromolecular pollutants. and other problems, to achieve the effect of saving natural clay resources, reducing head loss and high clay content
- Summary
- Abstract
- Description
- Claims
- Application Information
AI Technical Summary
Problems solved by technology
Method used
Image
Examples
Embodiment 1
[0021] Step 1) Prepare the mixture: the Bayer process red mud powder is made of the waste Bayer process red mud from Shandong Aluminum Factory, which is ground through a 120-mesh sieve. Grinding through a 120-mesh sieve, the mass percentage of clay in the river channel bottom mud is 70%, the mass percentage content of aquatic plants and algae is 9%, and the mass percentage of the main chemical components of Bayer process red mud, river channel bottom mud, and coal gangue powder for:
[0022]
[0023] Mix Bayer process red mud powder, river bottom mud powder, coal gangue powder, and pore-forming agent in a mass ratio of 50:40:5:5 to form a mixture, wherein the pore-forming agent is composed of coal powder, calcium carbonate powder and Sodium bicarbonate powder, the mass ratio of the three is: 2:2:1, and the particle size of the coal powder is 1-3mm.
[0024] Step 2) Add the mixed material into the disc granulator, and add water with 20% of the mixed material to granulate, a...
Embodiment 2
[0027] Step 1) Preparation of mixture: Bayer method red mud, river bottom mud, coal gangue powder, and pore-forming agent are the same as in Example 1, and the ratio of Bayer method red mud powder, river bottom mud powder, coal gangue powder, and pore-forming agent is 45:45 : 3:7 mass ratio mixed to form a mixture. Wherein the composition of the pore-forming agent is coal powder, calcium carbonate powder and sodium bicarbonate powder, the mass ratio of the three is: 4:2:1, and the particle diameter of the coal powder is the same as in Example 1.
[0028] Step 2) Add the mixture into the disc granulator, and add 22% water to granulate the mixture to obtain spherical particles.
[0029] Step 3) After drying the spherical particles in a drying oven at 100°C, put them into a muffle furnace for calcination. The sintering system is 0°C to 600°C and the heating rate is controlled at about 25°C / min. When the temperature reaches 600°C, keep the temperature for 15 minutes , the heati...
Embodiment 3
[0031] Step 1) Preparation of mixture: Bayer method red mud, river bottom mud, and pore-forming agent components are the same as in Example 1, and the Bayer method red mud powder, river bottom mud powder, coal gangue powder, and pore-forming agent are 40:50:0: The mass ratio of 10 is mixed to form a mixture. Wherein the composition of the pore-forming agent is coal powder, calcium carbonate powder and sodium bicarbonate powder, the mass ratio of the three is: 6:2.5:1.5, and the particle diameter of the coal powder is the same as in Example 1.
[0032] Step 2) Add the mixture into the disc granulator, and add 25% water to granulate the mixture to obtain spherical particles.
[0033] Step 3) After drying the spherical particles in a drying oven at 100°C, put them into a muffle furnace for calcination. The sintering system is from 0°C to 600°C and the heating rate is controlled at about 25°C / min. When the temperature reaches 600°C, keep the temperature for 10 minutes , the hea...
PUM
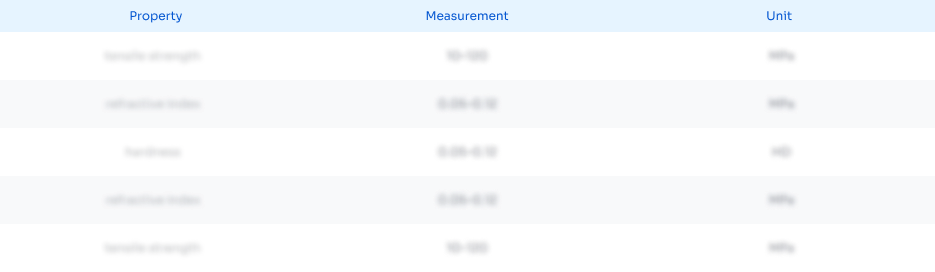
Abstract
Description
Claims
Application Information

- R&D Engineer
- R&D Manager
- IP Professional
- Industry Leading Data Capabilities
- Powerful AI technology
- Patent DNA Extraction
Browse by: Latest US Patents, China's latest patents, Technical Efficacy Thesaurus, Application Domain, Technology Topic, Popular Technical Reports.
© 2024 PatSnap. All rights reserved.Legal|Privacy policy|Modern Slavery Act Transparency Statement|Sitemap|About US| Contact US: help@patsnap.com