Method for purifying vanadium leaching solution
A technology for purifying impurity removal and leachate, applied in the direction of improving process efficiency, can solve the problems of unfavorable industrial continuous production, the purification effect needs to be improved, increasing the amount of acid added, etc., to meet the requirements of favorable treatment, acidity and impurity content Not high, the effect of reducing corrosion
- Summary
- Abstract
- Description
- Claims
- Application Information
AI Technical Summary
Problems solved by technology
Method used
Image
Examples
Embodiment 1
[0025] In this embodiment, phosphorus is removed in the vanadium slag clinker leaching process, and silicon is removed in the vanadium liquid.
[0026] Add 400g of clinker obtained by roasting the vanadium slag and additives in Table 1 into a 1000ml clean beaker, add 800ml of 80°C hot water for leaching and stirring, heat in a water bath to maintain this temperature, add 0.3g of magnesium sulfate, a small amount of sulfuric acid A solution made of ammonium and an appropriate amount of water, stirred for 10 minutes, stopped heating and stirring, left to stand for a period of time, then suction filtered, heated the filtrate to 80°C, added a solution made of 4.8g of aluminum sulfate and an appropriate amount of water, and adjusted the pH with sulfuric acid 8. After reacting for 10 minutes, cool down, let stand for 60 minutes, and filter to obtain [P]=5.65mg / L, [Si]=264.31mg / L vanadium liquid.
Embodiment 2
[0028] In this embodiment, phosphorus is removed in the vanadium slag clinker leaching process, and silicon is removed in the vanadium liquid.
[0029] Add 400g of clinker obtained by roasting vanadium slag and additives in Table 1 into a 1000ml clean beaker, add 800ml of 100°C hot water for leaching and stirring, heat in a water bath, add 0.38g of magnesium sulfate, a small amount of ammonium sulfate and an appropriate amount of The solution made of water was stirred for 15 minutes, the heating and stirring was stopped, and after standing for a period of time, it was suction filtered, the filtrate was heated to 100°C, the solution made of 4.5g of aluminum sulfate and an appropriate amount of water was added, and the pH was adjusted to 6.5 with sulfuric acid. After reacting for 15 minutes, cool down, let stand for 100 minutes, and filter to obtain [P]=4.60mg / L, [Si]=230.89mg / L vanadium liquid.
[0030] Table 1 The main chemical composition of a certain vanadium slag / g.L-1
...
Embodiment 3
[0033] This embodiment removes phosphorus and silicon from the vanadium slag leaching solution.
[0034] Add 800ml of vanadium leaching solution with concentration of 23.20g / L, phosphorus content of 25.82mg / L, silicon content of 432.38mg / L, pH8.5 into a 1000ml clean beaker, heat to 60°C, add 0.24g of magnesium sulfate, a small amount of ammonium sulfate and After stirring the solution made of appropriate amount of water for 5 minutes, add the solution made of 8.6g aluminum sulfate and appropriate amount of water, and adjust the pH to 7.0 with sulfuric acid. After reacting for 10 minutes, stop heating and stirring, cool to room temperature, and filter to obtain [P ]=7.53mg / L, [Si]=184.98mg / L vanadium solution.
PUM
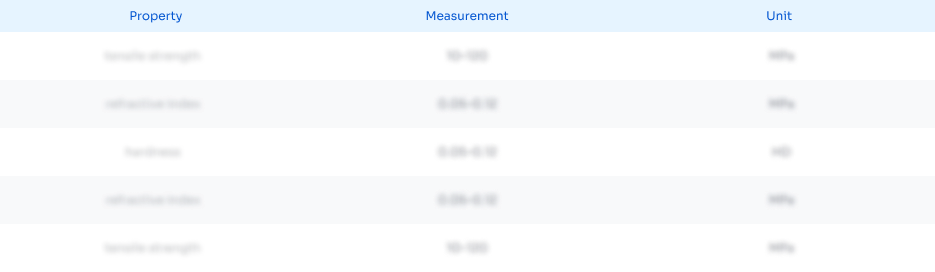
Abstract
Description
Claims
Application Information

- R&D Engineer
- R&D Manager
- IP Professional
- Industry Leading Data Capabilities
- Powerful AI technology
- Patent DNA Extraction
Browse by: Latest US Patents, China's latest patents, Technical Efficacy Thesaurus, Application Domain, Technology Topic, Popular Technical Reports.
© 2024 PatSnap. All rights reserved.Legal|Privacy policy|Modern Slavery Act Transparency Statement|Sitemap|About US| Contact US: help@patsnap.com