Method for manufacturing X70 steel-level large deformation-resistant longitudinally submerged arc welding pipe
A technology of anti-large deformation and straight seam submerged arc, which is applied in the field of welded pipe manufacturing to achieve uniform deformation and good roundness
- Summary
- Abstract
- Description
- Claims
- Application Information
AI Technical Summary
Problems solved by technology
Method used
Image
Examples
Embodiment 1
[0026] Example 1: Manufacture of Φ1016×21mm anti-large deformation steel pipe
[0027] 1. raw material
[0028] The X70 steel plate with a wall thickness of 21 mm is used, and its main alloy element content is shown in the table below.
[0029] Content of main alloying elements (mass percentage)
[0030] C mn Si P S Mo Ni+Cr+Cu V+ Nb+Ti Ceq Pcm 0.06 1.78 0.32 0.007 0.003 0.010 0.688 0.055 0.43 0.19
[0031] 2. Edge milling, after edge milling, the steel plate conforms to: the angle of the upper and lower grooves is 35°, and the height of the blunt edge is 5.5mm.
[0032] 3. Pre-bending, use the pre-bending machine to pre-bend the edge of the plate, and make the edge of the plate have a curvature that meets the requirements according to the requirements of the pipe diameter.
[0033] 4. JCO forming adopts the method of step-by-step pressing. The steel plate is fed 135mm each time. First, half of the steel plate is pressed 10 times...
Embodiment 2
[0060] Example 2: Manufacture of Φ1016×17.5mm anti-large deformation steel pipe
[0061] 1. raw material
[0062] The X70 steel plate with a wall thickness of 17.5 mm is used, and its main alloy element content is shown in the table below.
[0063] Content of main alloying elements (mass percentage)
[0064] C mn Si P S Mo Ni+Cr+Cu V+ Nb+Ti Ceq Pcm 0.05 1.68 0.25 0.006 0.002 0.012 0.69 0.065 0.42 0.19
[0065] 2. Edge milling, after edge milling, the steel plate conforms to: the angle of the upper and lower grooves is 35°, and the height of the blunt edge is 5.0mm.
[0066] 3. Pre-bending, use the pre-bending machine to pre-bend the edge of the plate, and make the edge of the plate have a curvature that meets the requirements according to the requirements of the pipe diameter.
[0067] 4. JCO molding adopts the method of step-by-step pressing. The steel plate is fed 123mm each time. First, half of the steel plate is pressed into ...
PUM
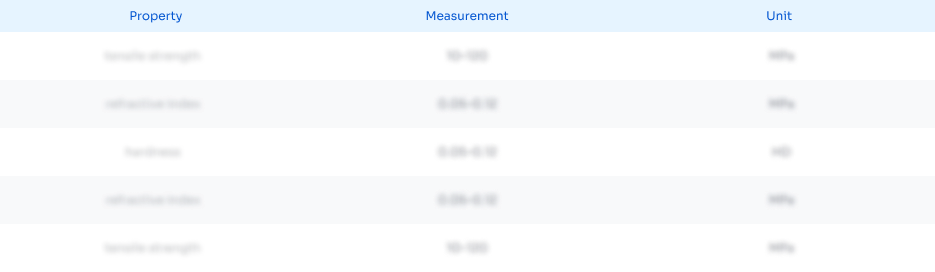
Abstract
Description
Claims
Application Information

- R&D
- Intellectual Property
- Life Sciences
- Materials
- Tech Scout
- Unparalleled Data Quality
- Higher Quality Content
- 60% Fewer Hallucinations
Browse by: Latest US Patents, China's latest patents, Technical Efficacy Thesaurus, Application Domain, Technology Topic, Popular Technical Reports.
© 2025 PatSnap. All rights reserved.Legal|Privacy policy|Modern Slavery Act Transparency Statement|Sitemap|About US| Contact US: help@patsnap.com