Preparation method of small complex magnetic shielding parts
A technology of magnetic shielding and parts, applied in the field of metal injection molding, can solve the problems of difficult machining, low hardness, long production cycle, etc. Effect
- Summary
- Abstract
- Description
- Claims
- Application Information
AI Technical Summary
Problems solved by technology
Method used
Image
Examples
example 1
[0033] Pure iron powder is selected, and polyethylene-paraffin-vegetable oil binder system is adopted. The formula is to take 40% polyethylene, 50% paraffin, and 10% vegetable oil by weight percentage; the volume ratio of feeding binder and raw material powder is 45%. :55 ratio. After the binder and the raw material powder are evenly mixed, the feed is granulated with a granulator; after the feed is granulated, it is injected on an injection molding machine at an injection temperature of 130°C, an injection pressure of 70 MPa, and an injection speed of 40 g / s. At a temperature of 40°C, it is processed into a blank to obtain a defect-free injection green body of the desired shape. The binder in the forming blank is removed by two-step degreasing method. Firstly, the blank is placed in methylene chloride to dissolve the paraffin and vegetable oil components; 3h, then heated to 800°C at a rate of 5°C / min for thermal degreasing and heat preservation for 12h; sintering was carried...
example 2
[0035]If the component is used in a weak magnetic field and requires a high magnetic shielding effect, the Fe-78%Ni permalloy with high magnetic permeability is selected. Prepare Fe-78%Ni mixed powder according to Fe:Ni mass fraction ratio of 22:78, and make uniform raw material mixed powder after ball milling for 8 hours. A polyethylene-paraffin-vegetable oil binder system is adopted, the formula of which is 20% polyethylene, 20% paraffin, and 60% vegetable oil by weight; the feed binder and raw material powder are mixed in a volume ratio of 35:65. After the binder and the raw material powder are evenly mixed, the feed is granulated with a granulator; after the feed is granulated, injection molding is performed on an injection molding machine at an injection temperature of 170°C, an injection pressure of 110 MPa, and an injection speed of 70 g / s. At a temperature of 70°C, it is processed into a blank, and a defect-free injection green body of the desired shape is obtained. T...
example 3
[0037] If the part is used in a strong magnetic field, a high-flux Fe-50% Ni permalloy is selected. Prepare Fe-50%Ni mixed powder according to Fe:Ni mass fraction ratio 50:50, and make uniform raw material mixed powder after ball milling for 8 hours. A polyethylene-paraffin-vegetable oil binder system is adopted, and the formula is as follows: 25% polyethylene, 25% paraffin, and 50% vegetable oil; the feed binder and raw material powder are mixed in a volume ratio of 45:55. After the binder and the raw material powder are evenly mixed, the feed is granulated with a granulator; after the feed is granulated, injection molding is performed on an injection molding machine at an injection temperature of 135°C, an injection pressure of 85 MPa, and an injection speed of 55 g / s. At a temperature of 50°C, it is processed into a blank to obtain a defect-free injection green body of the desired shape. The binder in the forming blank is removed by two-step degreasing method. Firstly, the...
PUM
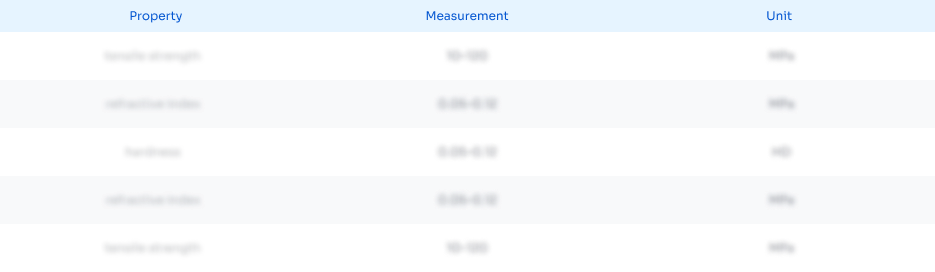
Abstract
Description
Claims
Application Information

- Generate Ideas
- Intellectual Property
- Life Sciences
- Materials
- Tech Scout
- Unparalleled Data Quality
- Higher Quality Content
- 60% Fewer Hallucinations
Browse by: Latest US Patents, China's latest patents, Technical Efficacy Thesaurus, Application Domain, Technology Topic, Popular Technical Reports.
© 2025 PatSnap. All rights reserved.Legal|Privacy policy|Modern Slavery Act Transparency Statement|Sitemap|About US| Contact US: help@patsnap.com