Method for controlling content of oxygen in steel
A technology of oxygen content and molten steel, applied in the field of iron and steel metallurgy, can solve the problems of inability to achieve metallurgical effect, difficulty in floating inclusions, deterioration of steel quality, etc., to avoid re-contamination, reduce the probability of inclusions, and improve casting performance.
- Summary
- Abstract
- Description
- Claims
- Application Information
AI Technical Summary
Problems solved by technology
Method used
Examples
Embodiment 1
[0037] Steelmaking using 70-ton high-impedance ultra-high power electric arc furnace, the process steps are as follows:
[0038] 1) Initially making molten steel in the electric furnace;
[0039] 2) During the tapping process, add a deoxidizer to the ladle for pre-deoxidation, and use bottom blowing argon to stir. The added deoxidizer is aluminum and silicon-aluminum-barium-calcium, and 2.3Kg of aluminum and 2.2Kg are added per ton of steel. Of silicon aluminum barium calcium;
[0040] 3) Lift the ladle containing molten steel to the refining station of the LF furnace, and no longer feed the aluminum wire for deoxidation. Add 12Kg of synthetic slag per ton of steel and heat it to create slag. Add 0.45Kg of calcium carbide per ton of steel for enhanced deoxidation. White slag is formed quickly, the total amount of FeO and MnO in the slag is 0.33wt%, and the slag basicity (%CaO / %SiO 2 ) Controlled at 5.5, the slag contains 28wt% Al 2 O 3 ;
[0041] 4) After the white slag retention tim...
Embodiment 2
[0045] Steelmaking using 70-ton high-impedance ultra-high power electric arc furnace, the process steps are as follows:
[0046] 1) Initially smelting molten steel in the electric furnace;
[0047] 2) During the tapping process, add a deoxidizer to the ladle for pre-deoxidation, and use bottom blowing argon to stir. The added deoxidizer is aluminum and silicon-aluminum-barium-calcium, and 2.5Kg of aluminum and 2.5Kg are added per ton of steel. Of silicon aluminum barium calcium;
[0048] 3) Lift the ladle containing molten steel to the refining station of the LF furnace, no longer feed the aluminum wire for deoxidation, add 13Kg of synthetic slag per ton of steel and heat it to create slag, and add 0.6Kg of calcium carbide per ton of steel for enhanced deoxidation. White slag is formed quickly, the total amount of FeO and MnO in the slag is 0.45wt%, and the slag basicity (%CaO / %SiO 2 ) Controlled at 5.9, the slag contains 32wt% Al 2 O 3 ;
[0049] 4) After the white slag retention ti...
Embodiment 3
[0053] Steelmaking using 70-ton high-impedance ultra-high power electric arc furnace, the process steps are as follows:
[0054] 1) Initially making molten steel in the electric furnace;
[0055] 2) During the tapping process, add a deoxidizer to the ladle for pre-deoxidation, and use bottom blowing argon to stir. The added deoxidizer is aluminum and silicon-aluminum-barium-calcium. Add 2.6Kg of aluminum and 2.0Kg per ton of steel. Of silicon aluminum barium calcium;
[0056] 3) Lift the ladle containing molten steel to the refining station of the LF furnace, and no longer feed the aluminum wire for deoxidation. Add 14Kg of synthetic slag per ton of steel and heat it to create slag, and add 0.7Kg of calcium carbide per ton of steel for enhanced deoxidation. White slag is formed quickly, the total amount of FeO and MnO in the slag is 0.40wt%, and the slag basicity (%CaO / %SiO 2 ) Controlled at 6.4, the slag contains 34wt% Al 2 O 3 ;
[0057] 4) After the white slag retention time is 20...
PUM
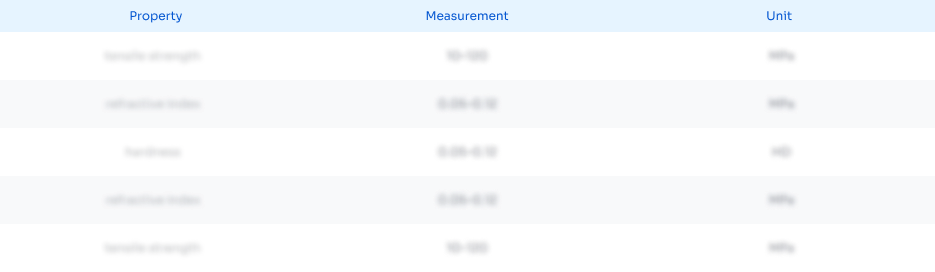
Abstract
Description
Claims
Application Information

- R&D
- Intellectual Property
- Life Sciences
- Materials
- Tech Scout
- Unparalleled Data Quality
- Higher Quality Content
- 60% Fewer Hallucinations
Browse by: Latest US Patents, China's latest patents, Technical Efficacy Thesaurus, Application Domain, Technology Topic, Popular Technical Reports.
© 2025 PatSnap. All rights reserved.Legal|Privacy policy|Modern Slavery Act Transparency Statement|Sitemap|About US| Contact US: help@patsnap.com