High glow-wire flame retardant reinforced PET/PA (polyethylene terephthalate/polyamide) alloy material and production method thereof
A high-glow-wire and alloy material technology, applied in the field of organic polymer materials, can solve problems such as poor glow-wire performance, and achieve the effects of high glow-wire performance and mechanical properties, simple production process, and good fluidity.
- Summary
- Abstract
- Description
- Claims
- Application Information
AI Technical Summary
Problems solved by technology
Method used
Image
Examples
Embodiment 1
[0011] Example 1: 30 kg of polyethylene terephthalate (PET) and 23 kg of polycaprolactam (PA) were dried at 130° C. for 4 hours. Pour the dried polyethylene terephthalate (PET) and polycaprolactam (PA) into a high-speed mixer and stir at a low speed. While stirring, add 6.5kg of toughening compatibilizer, 7kg of brominated flame retardant, 2kg of antimony trioxide, 1.2kg of zinc borate and 0.3kg of antioxidant, and stir for 2 minutes. Add the mixed raw materials into the twin-screw extruder and blend them for extrusion. The blending temperature is 245-260°C, the screw speed is 350r / min, 30kg of glass fiber is added to the glass fiber port, and the product is extruded, water-cooled, and pelletized. The produced material was dried at 120°C for 4 hours, and then standard mechanical property test specimens were prepared on an injection molding machine. The injection pressure is 60-90Mpa, the barrel temperature is 255-270°C, the mold temperature is 80°C, and the injection cycle i...
Embodiment 2
[0014] Example 2: 27kg of polyethylene terephthalate (PET) and 25kg of polycaprolactam (PA) were dried at 130°C for 4 hours. Pour the dried polyethylene terephthalate (PET) and polycaprolactam (PA) into a high-speed mixer and stir at a low speed. While stirring, add 6kg of toughening compatibilizer, 6.5kg of brominated flame retardant, 2kg of antimony trioxide, 1kg of zinc borate and 0.5kg of antioxidant, and stir for 2 minutes. Add the mixed raw materials into the twin-screw extruder and blend them for extrusion. The blending temperature is 245-260°C, the screw speed is 350r / min, 32kg of glass fiber is added to the glass fiber port, and the product is extruded, water-cooled, and pelletized. The produced material was dried at 120°C for 4 hours, and then standard mechanical property test specimens were prepared on an injection molding machine. The injection pressure is 60-90Mpa, the barrel temperature is 255-270°C, the mold temperature is 80°C, and the injection cycle is 40s....
PUM
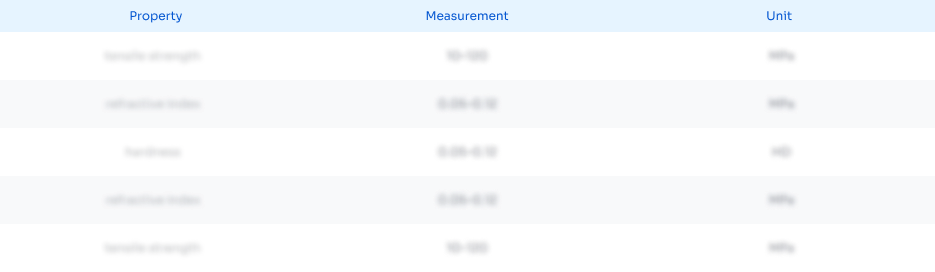
Abstract
Description
Claims
Application Information

- Generate Ideas
- Intellectual Property
- Life Sciences
- Materials
- Tech Scout
- Unparalleled Data Quality
- Higher Quality Content
- 60% Fewer Hallucinations
Browse by: Latest US Patents, China's latest patents, Technical Efficacy Thesaurus, Application Domain, Technology Topic, Popular Technical Reports.
© 2025 PatSnap. All rights reserved.Legal|Privacy policy|Modern Slavery Act Transparency Statement|Sitemap|About US| Contact US: help@patsnap.com