Polycrystalline silicon thin film and method for preparing polycrystalline silicon thin film by amorphous silicon low-temperature induction
A polysilicon thin film, low temperature induced technology, used in semiconductor devices, final product manufacturing, sustainable manufacturing/processing, etc., can solve the problems of slow crystallization rate of metal induction method, achieve increased crystallization rate, low nucleation barrier, contact The effect of increasing the area
- Summary
- Abstract
- Description
- Claims
- Application Information
AI Technical Summary
Problems solved by technology
Method used
Image
Examples
Embodiment 1
[0015] 1) Tin oxide transparent conductive glass (F-SNO 2 ) is the substrate 1, and a titanium silicide thin film layer and a titanium silicide nanowire composite structure are deposited on the substrate 1 by chemical vapor deposition. The titanium silicide nanowires include nanowires, nanonails, nanorods, and nanowire clusters, in the form of TiSi crystal Mutually;
[0016] 2) Depositing a 1 μm amorphous silicon film layer on the titanium silicide film and titanium silicide nanowire composite structure prepared in step 1) by plasma chemical vapor deposition at 13.56 MHz;
[0017] 3) Annealing and heat-treating the amorphous silicon thin film layer prepared in step 2) at 400° C. for 1 h, so that the titanium silicide nanowire induces the crystallization of the amorphous silicon thin film layer into a polycrystalline silicon thin film layer with large crystal grains, and finally obtains figure 1 Large grain polysilicon thin film shown.
Embodiment 2
[0019] 1) Using zinc oxide transparent conductive glass (Ag-ZnO) as the substrate, a layer of titanium silicide film and titanium silicide nanowire composite structure is deposited on the substrate 1 by chemical vapor deposition method. Titanium silicide nanowires include nanowires, nanonails, Rocket-shaped nanowires in the TiSi crystal phase;
[0020] 2) Depositing a layer of 2 μm amorphous silicon film layer on the titanium silicide film and titanium silicide nanowire composite structure prepared in step 1) by plasma chemical vapor deposition at 13.56MHZ;
[0021] 3) Annealing and heat-treating the amorphous silicon thin film layer prepared in step 2) at 400°C for 2 hours, so that the titanium silicide nanowires induce the crystallization of the amorphous silicon thin film layer into a polycrystalline silicon thin film layer with large grains, and finally obtain figure 1 Large grain polysilicon thin film shown.
Embodiment 3
[0023] 1) Tin oxide transparent conductive glass (F-SNO 2 ) is the substrate, and the titanium silicide nanowires are prepared on the substrate 1 by the solid-state reaction method. 2 crystal phase;
[0024] 2) Depositing a 3 μm amorphous silicon film layer on the titanium silicide nanowire prepared in step 1) by magnetron sputtering;
[0025] 3) The amorphous silicon thin film prepared in step 2) is annealed and heat-treated at 400°C for 2 hours, so that the titanium silicide nanowire induces the crystallization of the amorphous silicon thin film layer into a polycrystalline silicon thin film layer with large grains, and finally obtains figure 1 Large grain polysilicon thin film shown.
PUM
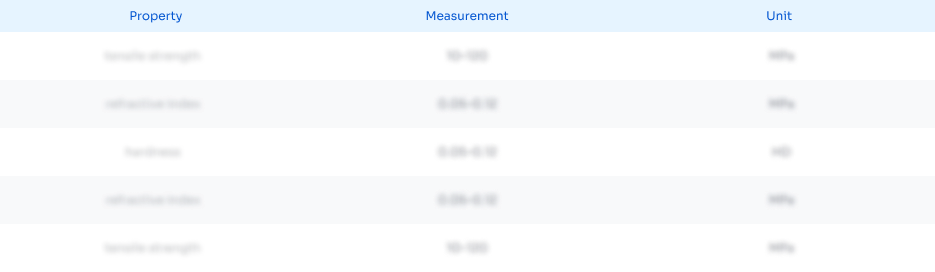
Abstract
Description
Claims
Application Information

- R&D
- Intellectual Property
- Life Sciences
- Materials
- Tech Scout
- Unparalleled Data Quality
- Higher Quality Content
- 60% Fewer Hallucinations
Browse by: Latest US Patents, China's latest patents, Technical Efficacy Thesaurus, Application Domain, Technology Topic, Popular Technical Reports.
© 2025 PatSnap. All rights reserved.Legal|Privacy policy|Modern Slavery Act Transparency Statement|Sitemap|About US| Contact US: help@patsnap.com