Nylon 6 slices for superfine sea-island fibers and manufacturing method thereof
A technology for sea-island fibers and a manufacturing method, which are applied in the field of nylon 6 slices for ultra-fine sea-island fibers and their manufacturing fields, can solve the problems affecting the uniformity of nylon 6 ultra-fine sea-island fibers, cannot guarantee the stability of melt viscosity, and the structure of ultra-fine sea-island fibers. Changes and other problems, to achieve the effect of reasonable ratio, good melt viscosity matching, and simple preparation process
- Summary
- Abstract
- Description
- Claims
- Application Information
AI Technical Summary
Problems solved by technology
Method used
Image
Examples
Embodiment 1
[0013] Add adipic acid, water, diaminodiphenylmethane, and isophthaloyldipiperidinamide in a ratio of 3:50:4.6:20, and melt them in a stainless steel container with a stirrer at 92-95°C, and then stir evenly. A mixed solution of additives is prepared.
[0014] The mixed solution of caprolactam solution and the above-mentioned additives is measured by a metering pump at a ratio of 1000:8, and then fed into a continuous polymerization reaction vessel for pre-pressurization polymerization-depressurization polymerization through a static mixer to carry out polymerization reaction. Under the conditions of pre-polymerization temperature 250-270°C and post-polymerization temperature 230-250°C, polymerize for 13-17 hours to obtain nylon 6 resin for ultra-fine island-in-the-sea fibers, and then the polymerized melt is continuously extruded into strips through a melt metering pump , pelletizing, continuous extraction, and continuous nitrogen drying to obtain nylon 6 slices for ultrafine...
Embodiment 2
[0016] Add adipic acid, water, diaminodiphenylmethane, and isophthaloyl dipiperidinium in a ratio of 2:50:5.5:30, and melt in a stainless steel mixing vessel with a stirrer at 92-95°C, then stir evenly , to prepare a mixed solution of additives.
[0017] A certain amount of caprolactam solution and the above auxiliary agent mixed solution are metered by a metering pump at a ratio of 1000:8.9, and then put into a continuous polymerization reactor for pre-pressurization polymerization-decompression polymerization polymerization through a static mixer to carry out polymerization reaction. Under the conditions of pre-polymerization temperature 250-270°C and post-polymerization temperature 230-250°C, polymerize for 13-17 hours to obtain nylon 6 resin for ultra-fine island-in-the-sea fibers, and then the polymerized melt is continuously extruded into strips through a melt metering pump , pelletizing, continuous extraction, and continuous nitrogen drying to obtain nylon 6 slices for ...
PUM
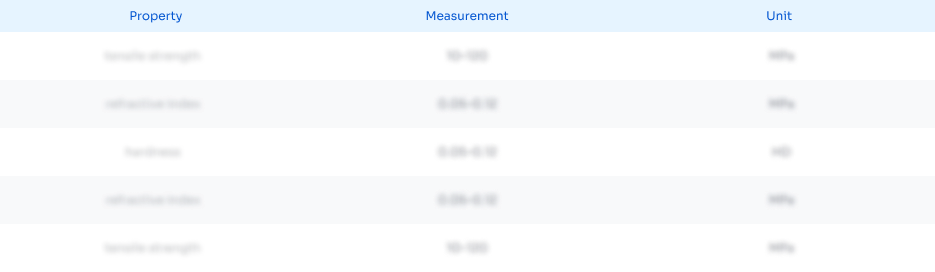
Abstract
Description
Claims
Application Information

- R&D
- Intellectual Property
- Life Sciences
- Materials
- Tech Scout
- Unparalleled Data Quality
- Higher Quality Content
- 60% Fewer Hallucinations
Browse by: Latest US Patents, China's latest patents, Technical Efficacy Thesaurus, Application Domain, Technology Topic, Popular Technical Reports.
© 2025 PatSnap. All rights reserved.Legal|Privacy policy|Modern Slavery Act Transparency Statement|Sitemap|About US| Contact US: help@patsnap.com